Forging process of stepped shaft with large diameter differences
A stepped shaft, a relatively large technology, applied in the forging process of stepped shafts, can solve the problems of long processing time, low production efficiency, waste of materials, etc., and achieve the effect of improving productivity
- Summary
- Abstract
- Description
- Claims
- Application Information
AI Technical Summary
Problems solved by technology
Method used
Image
Examples
Embodiment Construction
[0013] The specific content of the present invention will be described in detail below with reference to the drawings and specific embodiments.
[0014] Such as figure 1 , figure 2 As shown, a forging process of stepped shafts with large diameter differences includes the following process steps: blanking, shot blasting, first heating, coating, second heating, forward extrusion, forming, stress relief annealing, polishing Saponify pellets, reduce diameter, and take end faces.
[0015] In this embodiment: the cutting: according to the selected diameter of the round steel, a circular saw is used to saw the material, and the weight of the saw material is the weight of the forging blank. The first heating: the bar is heated by induction intermediate frequency heating to 600-650°C; the second heating: the bar is heated by induction intermediate frequency heating to 800 -820°C. The forward extrusion: under the pressure of the hydraulic press, two steps d3 and d4 are extruded, and the ...
PUM
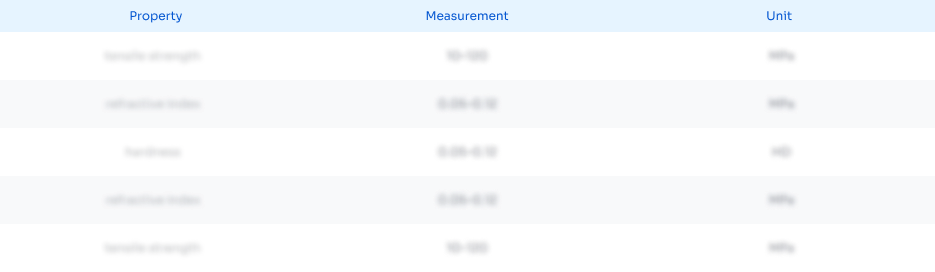
Abstract
Description
Claims
Application Information

- R&D Engineer
- R&D Manager
- IP Professional
- Industry Leading Data Capabilities
- Powerful AI technology
- Patent DNA Extraction
Browse by: Latest US Patents, China's latest patents, Technical Efficacy Thesaurus, Application Domain, Technology Topic, Popular Technical Reports.
© 2024 PatSnap. All rights reserved.Legal|Privacy policy|Modern Slavery Act Transparency Statement|Sitemap|About US| Contact US: help@patsnap.com