Active control device for propeller shaft transverse vibration
A technology of lateral vibration and active control, applied in the direction of propulsion transmission, transmission with synchronous propulsion components, propulsion power transmission, etc., can solve the problems of narrow operating frequency band, limited vibration damping effect, and inability to adapt to changes, etc., to achieve Improve working conditions, reduce friction and wear, reduce coupling vibration and sound radiation effects
- Summary
- Abstract
- Description
- Claims
- Application Information
AI Technical Summary
Problems solved by technology
Method used
Image
Examples
Embodiment 1
[0025] The electromagnetic bearing includes two pairs of electromagnet assemblies, four electromagnets are evenly distributed along the circumference, and the two sets of electromagnet assemblies are respectively used to control the vibration of the electromagnetic bearing in the vertical and horizontal directions. The electromagnet has a U-shaped structure, and each electromagnet includes two magnetic poles.
[0026] The control of the two electromagnets of each pair of electromagnet assemblies can adopt a differential drive mode, where the electromagnetic force of one electromagnet is driven by the sum of the bias current and the control current, and the electromagnetic force of the other electromagnet is controlled by the bias current and the control current. Driven by the difference of current, the total electromagnetic control force of the group of electromagnet components is the difference of the electromagnetic force of the two electromagnets. The bias current is the DC...
PUM
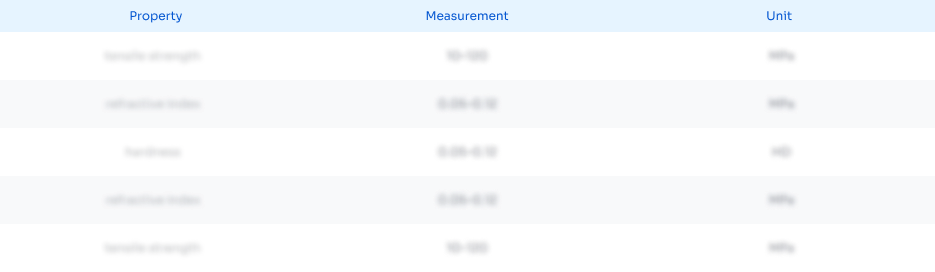
Abstract
Description
Claims
Application Information

- R&D
- Intellectual Property
- Life Sciences
- Materials
- Tech Scout
- Unparalleled Data Quality
- Higher Quality Content
- 60% Fewer Hallucinations
Browse by: Latest US Patents, China's latest patents, Technical Efficacy Thesaurus, Application Domain, Technology Topic, Popular Technical Reports.
© 2025 PatSnap. All rights reserved.Legal|Privacy policy|Modern Slavery Act Transparency Statement|Sitemap|About US| Contact US: help@patsnap.com