Mixing tank structure of fracturing blender truck
A technology for mixing tanks and sand mixers, which is applied in the direction of mixer accessories, mixers, dissolving, etc. It can solve problems such as excessive vortex, discharge centrifugal pump impact, and large discharge pressure fluctuations, so as to promote stability, relieve kinetic energy, The effect of reducing kinetic energy
- Summary
- Abstract
- Description
- Claims
- Application Information
AI Technical Summary
Problems solved by technology
Method used
Image
Examples
Embodiment 1
[0036] A mixing tank structure of a sand mixer, such as Figure 1 to Figure 5 As shown, a tank body is included, the tank body includes a tank bottom plate 1 and a tank inner layer 3 and a tank outer layer 2 arranged on the tank bottom plate, the tank bottom plate 1 and the tank inner layer 3 form a stirring cavity 4, There is a gap between the tank inner layer 3 and the tank outer layer 2 to form a tank layer gap, the tank outer layer is provided with a liquid inlet 5, the tank inner layer is provided with a liquid outlet, and the liquid inlet The mouth, the gap between the tank layers and the liquid outlet are connected to form a liquid inlet channel. The bottom of the tank body is also provided with a liquid discharge channel, through which the liquid is introduced into the tank, and then discharged through the liquid discharge channel.
[0037] In this embodiment, in the design of the whole structure, the figure 2 It is an illustration of the flow direction of the liquid...
Embodiment 2
[0056] On the basis of the above-mentioned embodiment 1, the design of the liquid outlet not only adopts the above three fixed (upper, middle, lower) design methods, but the main purpose of the design of the liquid outlet is to introduce liquid into the tank , and in the design of this structure, in this embodiment, as follows:
[0057] Based on the design of the above specific structure, as a further optimized design, the liquid outlet includes the upper liquid outlet 6 and the middle liquid outlet 7, or the liquid outlet includes the upper liquid outlet 6 and the lower liquid outlet port 8, or, the liquid outlet includes middle liquid outlet 7 and lower liquid outlet 8;
[0058] Wherein, the upper liquid outlet 6 is also provided with an upper water baffle 20, and the upper liquid outlet 6 is formed with the water baffle 15, the tank inner layer 3 and the tank outer layer 2 as side walls, or, the The upper liquid outlet 6 is a plurality of liquid outlets opened on the upper...
Embodiment 3
[0063] Similar to Example 2, but on the basis of the above, the design of the liquid outlet can be one of them. Specifically, based on the design of the above-mentioned specific structure, as a further optimized design, the liquid outlet includes the above Liquid outlet 6 or middle liquid outlet 7 or lower liquid outlet 8;
[0064] Wherein, the upper liquid outlet 6 is also provided with an upper water baffle 20, and the upper liquid outlet 6 is formed with the water baffle 15, the tank inner layer 3 and the tank outer layer 2 as side walls, or, the The upper liquid outlet 6 is a plurality of liquid outlets opened on the upper part of the inner layer 3 of the tank;
[0065] The middle liquid outlet 7 is a plurality of liquid outlets opened in the middle of the inner layer of the tank;
[0066] The lower liquid outlet 8 is a plurality of liquid outlets opened in the lower part of the inner layer of the tank.
PUM
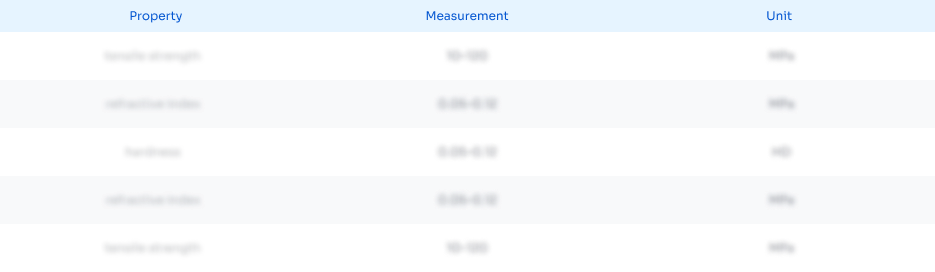
Abstract
Description
Claims
Application Information

- R&D Engineer
- R&D Manager
- IP Professional
- Industry Leading Data Capabilities
- Powerful AI technology
- Patent DNA Extraction
Browse by: Latest US Patents, China's latest patents, Technical Efficacy Thesaurus, Application Domain, Technology Topic, Popular Technical Reports.
© 2024 PatSnap. All rights reserved.Legal|Privacy policy|Modern Slavery Act Transparency Statement|Sitemap|About US| Contact US: help@patsnap.com