Industrial safety laser simultaneous localization and mapping (SLAM) navigation pallet stacking automated guided vehicle (AGV)
An industrial safety and stacking technology, applied in the direction of hoisting equipment safety devices, lifting devices, etc., can solve the problems of regular maintenance, high cost, long construction period, etc., and achieve the effect of ensuring safety, low cost and simple structure
- Summary
- Abstract
- Description
- Claims
- Application Information
AI Technical Summary
Problems solved by technology
Method used
Image
Examples
Embodiment Construction
[0034] In order to make the purpose, technical solutions and advantages of the embodiments of the present invention more clear, the technical solutions in the embodiments of the present invention will be clearly and completely described below in conjunction with the drawings in the embodiments of the present invention. Apparently, the described embodiments are some, but not all, embodiments of the present invention. Based on the embodiments of the present invention, all other embodiments obtained by persons of ordinary skill in the art without creative efforts fall within the protection scope of the present invention.
[0035] An industrial safe laser SLAM navigation pallet stacking AGV, such as Figure 1 to Figure 8 As shown, it includes a vehicle frame 101, a lower cover 102 fixed to the front end of the vehicle frame 101, an upper cover 103 fixed between the top of the vehicle frame 101 and the top of the lower cover 102, a laser SLAM navigation system, and a vehicle drive ...
PUM
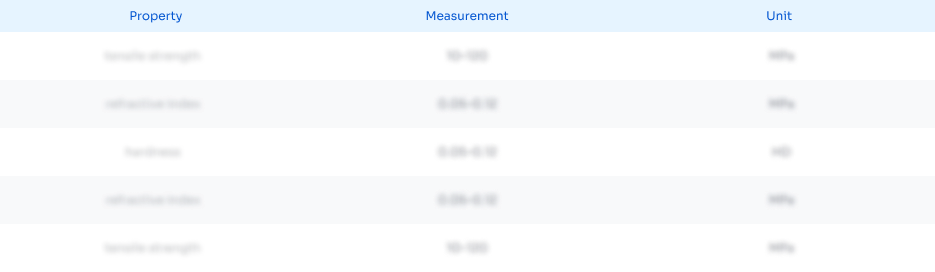
Abstract
Description
Claims
Application Information

- R&D
- Intellectual Property
- Life Sciences
- Materials
- Tech Scout
- Unparalleled Data Quality
- Higher Quality Content
- 60% Fewer Hallucinations
Browse by: Latest US Patents, China's latest patents, Technical Efficacy Thesaurus, Application Domain, Technology Topic, Popular Technical Reports.
© 2025 PatSnap. All rights reserved.Legal|Privacy policy|Modern Slavery Act Transparency Statement|Sitemap|About US| Contact US: help@patsnap.com