A rail transit catenary compensation monitoring device and monitoring method
A rail transit and catenary technology, applied in the field of rail transit, can solve the problems of unfavorable construction and maintenance, uneconomical, low precision, etc., to facilitate analysis and prediction, reduce maintenance costs, and prevent major accidents.
- Summary
- Abstract
- Description
- Claims
- Application Information
AI Technical Summary
Problems solved by technology
Method used
Image
Examples
Embodiment Construction
[0017] Such as figure 1 As shown, the special monitoring equipment for the electrified railway catenary anchor compensation device described in the present application includes horizontal upper brackets 4 and The horizontal lower bracket 5, the horizontal upper bracket 4 and the horizontal lower bracket 5 can be fixed on the pillar 3 by hook bolts; since the contact line 1 and the catenary cable 2 fixed on the pillar are often the contact line 1 below and the catenary cable 2 on the Therefore, the horizontal upper bracket 5 should be located on the upper part of the contact line counterweight 6 and catenary cable counterweight 7 close to the traction pulley block on the contact line 1, and the horizontal lower support 5 should be located at the contact line counterweight 6 and catenary cable The bottom of the counterweight 7 is close to the ground.
[0018] A first distance measuring sensor 8 and a second distance measuring sensor 9 are arranged on the horizontal support 4, a...
PUM
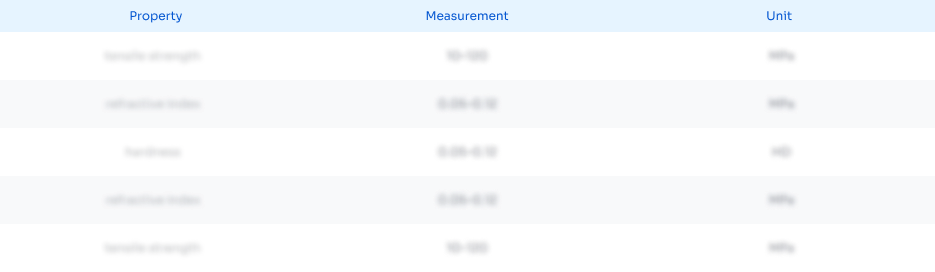
Abstract
Description
Claims
Application Information

- R&D
- Intellectual Property
- Life Sciences
- Materials
- Tech Scout
- Unparalleled Data Quality
- Higher Quality Content
- 60% Fewer Hallucinations
Browse by: Latest US Patents, China's latest patents, Technical Efficacy Thesaurus, Application Domain, Technology Topic, Popular Technical Reports.
© 2025 PatSnap. All rights reserved.Legal|Privacy policy|Modern Slavery Act Transparency Statement|Sitemap|About US| Contact US: help@patsnap.com