Integral taphole clay jacket pouring installation method and blast furnace taphole structure
A technology of iron hole mud jacket and installation method, which is applied in the direction of blast furnace, blast furnace details, blast furnace parts, etc., can solve the problems of long shutdown time of blast furnace, reduce blast furnace shutdown rate, quickly replace mud jacket operations, and reduce blast furnace The effect of wind break time
- Summary
- Abstract
- Description
- Claims
- Application Information
AI Technical Summary
Problems solved by technology
Method used
Image
Examples
Embodiment 1
[0054] Such as figure 1 As shown, the embodiment of the present application provides a method for pouring and installing an integral iron hole mud sleeve, which includes the following steps:
[0055] Step S100: Prepare the mud casing castable;
[0056] Step S200: making a clay sleeve mold;
[0057] Step S300: casting and forming the mud jacket with the help of the mud jacket mold;
[0058] Step S400: taking out the mud jacket from the mud jacket mold and drying;
[0059] Step S500: Put the mud sleeve into a plastic bag and seal it;
[0060] Step S600: cleaning up the old material of the mud jacket to form a mud jacket frame;
[0061] Step S700: apply adhesive around the mud sleeve frame;
[0062]Step S800: put the dried mud jacket into the mud jacket frame and glue it with an adhesive;
[0063] Step S900: Proofreading the mud cover.
[0064] It should be noted that step 100 can be performed before step S200, or after step S200 and before step S300, that is to say, as lo...
PUM
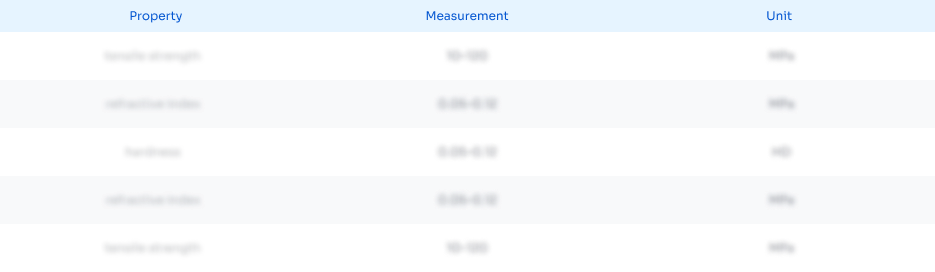
Abstract
Description
Claims
Application Information

- R&D
- Intellectual Property
- Life Sciences
- Materials
- Tech Scout
- Unparalleled Data Quality
- Higher Quality Content
- 60% Fewer Hallucinations
Browse by: Latest US Patents, China's latest patents, Technical Efficacy Thesaurus, Application Domain, Technology Topic, Popular Technical Reports.
© 2025 PatSnap. All rights reserved.Legal|Privacy policy|Modern Slavery Act Transparency Statement|Sitemap|About US| Contact US: help@patsnap.com