Water-based acrylic acid dispersion applied to high-speed rail surface coating, and preparation method thereof
A water-based acrylic and surface coating technology, applied in the direction of coating, can solve the problems of low solid content, high viscosity, difficult to break through high solid content, etc., and achieve the effect of high viscosity and low VOC content
- Summary
- Abstract
- Description
- Claims
- Application Information
AI Technical Summary
Problems solved by technology
Method used
Image
Examples
Embodiment 1
[0024] The aqueous acrylic dispersion comprises 10 parts of reactive polyol solvents containing double bonds, 46 parts of monomers and chain transfer agents, 40 parts of deionized water and 4 parts of dimethylethanolamine in parts by mass.
[0025] Preferably, the monomers include 10 parts by mass of methyl methacrylate, 8 parts of hydroxyethyl acrylate, and 18 parts of styrene;
[0026] Preferably, the chain transfer agent butyl acrylate is 10 parts by mass;
[0027] Preferably, the double bond reactive polyol solvent is polyvinyl alcohol.
[0028] The present invention also provides a kind of preparation method that is applied to the aqueous acrylic acid dispersion of high iron surface coating, and it comprises:
[0029] Step 1, putting the reactive polyol solvent containing the double bond into the reaction kettle in required mass percentage;
[0030] Step 2. Close the feeding hole, turn on the nitrogen to replace the air in the kettle, and start to raise the temperature ...
Embodiment 2
[0034] The aqueous acrylic dispersion comprises 12 parts of a double bond-containing reactive polyol solvent, 46 parts of a monomer and a chain transfer agent, 40 parts of deionized water and 2 parts of dimethylethanolamine in parts by mass.
[0035] Preferably, the monomers include 10 parts by mass of methyl methacrylate, 8 parts of hydroxyethyl acrylate, and 18 parts of styrene;
[0036] Preferably, the chain transfer agent butyl acrylate is 10 parts by mass;
[0037] Preferably, the double bond reactive polyol solvent is polyvinyl alcohol.
[0038] The present invention also provides a kind of preparation method that is applied to the aqueous acrylic acid dispersion of high iron surface coating, and it comprises:
[0039] Step 1, putting the reactive polyol solvent containing the double bond into the reaction kettle in required mass percentage;
[0040] Step 2. Close the feeding hole, turn on the nitrogen to replace the air in the kettle, and start to raise the temperatur...
Embodiment 3
[0044] The aqueous acrylic dispersion comprises 10 parts of reactive polyol solvents containing double bonds, 46 parts of monomers and chain transfer agents, 40 parts of deionized water and 4 parts of dimethylethanolamine in parts by mass.
[0045] Preferably, the monomers include 12 parts of methyl methacrylate, 8 parts of hydroxyethyl acrylate, and 16 parts of styrene in parts by mass;
[0046] Preferably, the chain transfer agent butyl acrylate is 10 parts by mass;
[0047] Preferably, the double bond reactive polyol solvent is polyvinyl alcohol.
[0048] The present invention also provides a kind of preparation method that is applied to the aqueous acrylic acid dispersion of high iron surface coating, and it comprises:
[0049] Step 1, putting the reactive polyol solvent containing the double bond into the reaction kettle in required mass percentage;
[0050] Step 2. Close the feeding hole, turn on the nitrogen to replace the air in the kettle, and start to raise the tem...
PUM
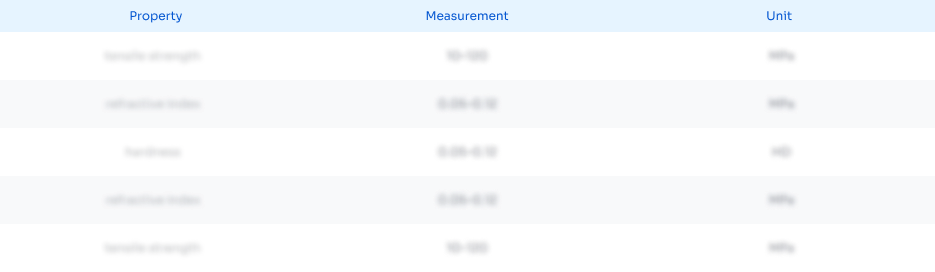
Abstract
Description
Claims
Application Information

- R&D Engineer
- R&D Manager
- IP Professional
- Industry Leading Data Capabilities
- Powerful AI technology
- Patent DNA Extraction
Browse by: Latest US Patents, China's latest patents, Technical Efficacy Thesaurus, Application Domain, Technology Topic, Popular Technical Reports.
© 2024 PatSnap. All rights reserved.Legal|Privacy policy|Modern Slavery Act Transparency Statement|Sitemap|About US| Contact US: help@patsnap.com