Lake sediment curing agent
A curing agent and bottom sludge technology, which is applied in the fields of fixed/solidified sludge treatment, polluted waterway/lake/pond/river treatment, sludge treatment, etc. It can solve the problem of poor curing effect of high water content bottom sludge and unfavorable resource utilization The utilization of the soil, the high pH value of the solidified soil, etc., to achieve the effect of being beneficial to resource utilization, reducing water content, and good adsorption performance
- Summary
- Abstract
- Description
- Claims
- Application Information
AI Technical Summary
Problems solved by technology
Method used
Examples
Embodiment 1
[0022] Activation of shell powder: After cleaning the collected oyster shells, soak them in 0.2mol / L sodium hydroxide solution for 1 hour, remove them and wash them with deionized water until the washing solution is neutral, then dry and grind them. Pass through a 100-mesh sieve, then place it in a muffle furnace for calcination at a temperature of 450°C for 1 hour, cool with the furnace, take it out, and place it in a ball mill to grind to obtain nano-shell powder. Liquid ratio stirring and dispersing in deionized water, ultrasonication for 1h under the condition of frequency 48KHz, power 800W, and then spray drying under the conditions of inlet atmosphere temperature of 200°C, outlet atmosphere temperature of 100°C, flow rate of 500ml / h Granulating to obtain activated shell powder.
[0023] Preparation of porous shell powder: Weigh 15g of activated shell powder and add it to 20g of phenolic resin, stir and mix for 40 minutes, heat to 110°C, and keep it warm for 30 minutes. A...
Embodiment 2
[0027] Activation of shell powder: After cleaning the collected oyster shells, soak them in 0.2mol / L sodium hydroxide solution for 1 hour, remove them and wash them with deionized water until the washing solution is neutral, then dry and grind them. Pass through a 100-mesh sieve, then place it in a muffle furnace for calcination at a temperature of 480°C for 1 hour, cool with the furnace, take it out, and place it in a ball mill to grind to obtain nano-shell powder. Disperse in deionized water with liquid ratio stirring, ultrasonicate for 1h under the condition of frequency 40KHz, power 1000W, and then spray dry under the conditions of inlet atmosphere temperature of 200°C, outlet atmosphere temperature of 100°C, flow rate of 500ml / h Granulating to obtain activated shell powder.
[0028]Preparation of porous shell powder: Weigh 18g of activated shell powder and add it to 32g of phenolic resin, stir and mix for 45 minutes, heat to 105°C, and keep it warm for 40 minutes. After t...
Embodiment 3
[0032] Activation of shell powder: After cleaning the collected oyster shells, soak them in 0.2mol / L sodium hydroxide solution for 1 hour, remove them and wash them with deionized water until the washing solution is neutral, then dry and grind them. Pass through a 100-mesh sieve, then place it in a muffle furnace for calcination at a temperature of 500°C for 1 hour, cool with the furnace, take it out, and place it in a ball mill to grind to obtain nano-shell powder. Liquid ratio stirring and dispersing in deionized water, ultrasonication for 1h under the condition of frequency 50KHz, power 800W, and then spray drying under the conditions of inlet atmosphere temperature of 200°C, outlet atmosphere temperature of 100°C, flow rate of 500ml / h Granulating to obtain activated shell powder.
[0033] Preparation of porous shell powder: Weigh 10g of activated shell powder and add it to 18g of phenolic resin, stir and mix for 30 minutes, heat to 100°C, and keep it warm for 45 minutes to...
PUM
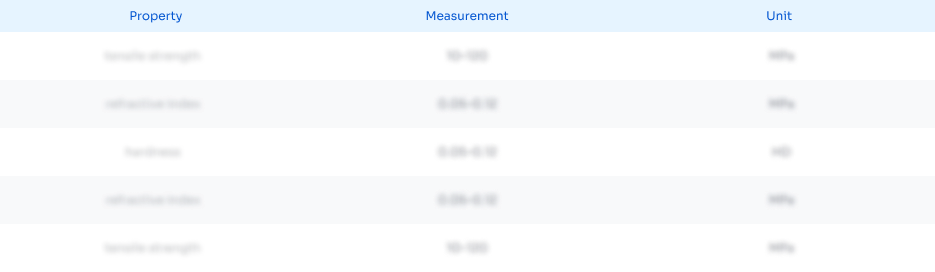
Abstract
Description
Claims
Application Information

- R&D
- Intellectual Property
- Life Sciences
- Materials
- Tech Scout
- Unparalleled Data Quality
- Higher Quality Content
- 60% Fewer Hallucinations
Browse by: Latest US Patents, China's latest patents, Technical Efficacy Thesaurus, Application Domain, Technology Topic, Popular Technical Reports.
© 2025 PatSnap. All rights reserved.Legal|Privacy policy|Modern Slavery Act Transparency Statement|Sitemap|About US| Contact US: help@patsnap.com