Wear-resistant conductive polyamide composite material and preparation method thereof
A composite material and polyamide technology, which is applied in the field of wear-resistant conductive polyamide composite materials and its preparation, to achieve the effects of improving service life, high color matching freedom, and improving wear resistance
- Summary
- Abstract
- Description
- Claims
- Application Information
AI Technical Summary
Problems solved by technology
Method used
Image
Examples
preparation example Construction
[0033] Preparation of modified solution: Add 200mL of 5% silver nitrate solution into a beaker, then slowly add excess 1% sodium hydroxide aqueous solution, and keep stirring for 10min to react. Take out the precipitate and put it in a clean beaker, slowly add 80ml of 3% ammonia water dropwise to dissolve the precipitate;
[0034] Modification of glass fiber: put the treated glass fiber into 80ml of modification solution, put no more than 50g of glass fiber into it, ultrasonically disperse while stirring constantly to suspend the glass fiber fully in the solution, then slowly add in drops 80ml of 10% glucose aqueous solution is reacted in a hot water bath at 65° C. for more than 10 minutes, washed with water and filtered to obtain a modified glass fiber coated with silver on the surface.
Embodiment 1
[0036] (1) Prepare materials according to the following components and parts by weight:
[0037]
[0038] Among them, the matrix resin is PA6 CM1017 of Toray Corporation of Japan;
[0039] Wear-resisting agent is polytetrafluoroethylene PTFE, micron grade, commercially available;
[0040] The antioxidant is Irganox B900;
[0041] The lubricant is polyethylene wax;
[0042] (2) Mix the above-mentioned raw materials except glass fiber into the high-speed mixer according to the above ratio and stir. After mixing evenly, feed it into the twin-screw extruder through the metering device. The glass fiber is processed by side feeding, and the barrel temperature is set. The temperature is 200°C-240°C, through shearing and plasticizing, mixing the materials evenly, and then granulating to obtain the desired wear-resistant conductive polyamide composition.
Embodiment 2
[0044] (1) Prepare materials according to the following components and parts by weight:
[0045]
[0046] Among them, the matrix resin is PA6 CM1017 of Toray Corporation of Japan;
[0047] Wear-resisting agent is polytetrafluoroethylene PTFE, micron grade, commercially available;
[0048] The antioxidant is Irganox B900;
[0049] The lubricant is polyethylene wax;
[0050] (2) Mix the above-mentioned raw materials except glass fiber into the high-speed mixer according to the above ratio and stir. After mixing evenly, feed it into the twin-screw extruder through the metering device. The glass fiber is processed by side feeding, and the barrel temperature is set. The temperature is 200°C-240°C, through shearing and plasticizing, mixing the materials evenly, and then granulating to obtain the desired wear-resistant conductive polyamide composition.
PUM
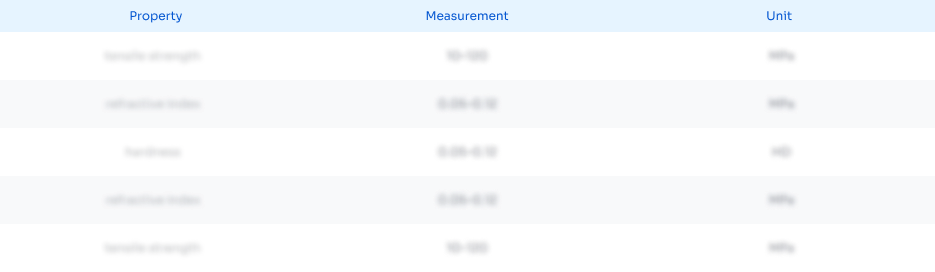
Abstract
Description
Claims
Application Information

- R&D Engineer
- R&D Manager
- IP Professional
- Industry Leading Data Capabilities
- Powerful AI technology
- Patent DNA Extraction
Browse by: Latest US Patents, China's latest patents, Technical Efficacy Thesaurus, Application Domain, Technology Topic, Popular Technical Reports.
© 2024 PatSnap. All rights reserved.Legal|Privacy policy|Modern Slavery Act Transparency Statement|Sitemap|About US| Contact US: help@patsnap.com