MEMS piezoelectric piezoelectric sound pressure sensing chip based on elastic beam structures
An elastic beam, pressure sensing technology, applied in the direction of using electrical devices, electromagnetic means, vibration measurement in fluids, etc., can solve the problems of poor performance of MEMS sound pressure sensor chips, complex processing technology, large chip size, etc. Achieve the effect of improving acceleration sensitivity, increasing sensitivity, and increasing sensitivity
- Summary
- Abstract
- Description
- Claims
- Application Information
AI Technical Summary
Problems solved by technology
Method used
Image
Examples
Embodiment Construction
[0041] In the following description, specific details such as specific system structures and technologies are presented for the purpose of illustration rather than limitation, so as to thoroughly understand the embodiments of the present invention. It will be apparent, however, to one skilled in the art that the invention may be practiced in other embodiments without these specific details. In other instances, detailed descriptions of well-known systems, devices, circuits, and methods are omitted so as not to obscure the description of the present invention with unnecessary detail.
[0042] In order to illustrate the technical solutions of the present invention, specific examples are used below to illustrate.
[0043] figure 1 The structural schematic diagram of the MEMS piezoelectric acoustic pressure sensor chip based on the elastic beam structure provided by the embodiment of the present invention is described in detail as follows.
[0044] see Figure 1 to Figure 3 , a ...
PUM
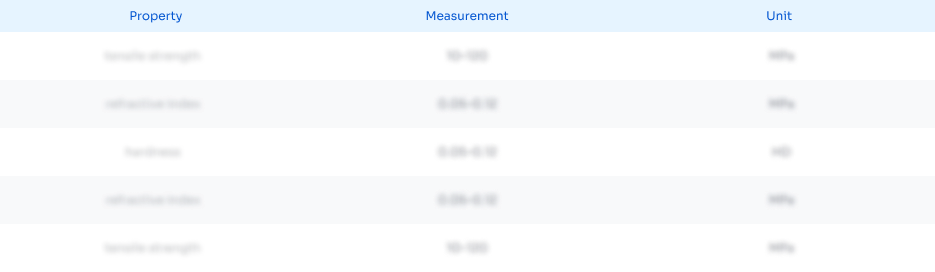
Abstract
Description
Claims
Application Information

- R&D Engineer
- R&D Manager
- IP Professional
- Industry Leading Data Capabilities
- Powerful AI technology
- Patent DNA Extraction
Browse by: Latest US Patents, China's latest patents, Technical Efficacy Thesaurus, Application Domain, Technology Topic, Popular Technical Reports.
© 2024 PatSnap. All rights reserved.Legal|Privacy policy|Modern Slavery Act Transparency Statement|Sitemap|About US| Contact US: help@patsnap.com