Distribution box door plate bevel edge process
A distribution box and door panel technology, which is applied in the field of the bevel edge process of the distribution box door panel, can solve the problems of reduced production efficiency, many punching and punching process steps, etc., and achieves the effect of improving quality
- Summary
- Abstract
- Description
- Claims
- Application Information
AI Technical Summary
Problems solved by technology
Method used
Image
Examples
Embodiment 1
[0037] Embodiment 1 is basically as attached figure 1 with figure 2 Shown:
[0038] The beveled edge process of the door panel of the distribution box adopts a special mold for the beveled edge. The special mold includes an upper die head 10 and a lower die base 11. There are two punch faces at the bottom of the upper die head 10, and the two punch faces are opposite to the upper die head. The center line of the die head 10 is arranged symmetrically, wherein the convex die surface includes a raised edge 12 and side edges 13 arranged on both sides of the raised edge 12, the raised edge 12 and the side edge 13 are horizontally arranged, and the raised edge 12 and the side edge 13 are arranged horizontally. A hypotenuse 14 is formed between the sides 13, and the included angle between the hypotenuse 14 and the horizontal plane is not less than 30°, and in this application, the included angle is 33°.
[0039] On the raised edge 12, a plurality of hole punches 15 are fixed, and ...
Embodiment 2
[0049] Embodiment 2 is basically as attached Figure 4 Shown:
[0050] The difference from Embodiment 1 is that the load-bearing plate 20 is slidably connected in the first accommodation chamber 18, and a plurality of support frames 25 are fixed at the bottom of the first accommodation chamber 18, gaps are formed between adjacent support frames 25, and The width of the slit is greater than the aperture of the blanking hole 21, and a plurality of elastic members 26 are fixed between the load-bearing plate 20 and the support frame 25. When the load-bearing plate 20 is not stressed, its top surface exceeds the bottom surface of the die groove 17. In order to prevent The load-bearing plate 20 shakes, the load-bearing plate 20 is set as a rectangular plate, and a plurality of limit blocks 27 are fixed on the side 13 of the load-bearing plate 20, and the multiple limit blocks 27 are evenly distributed on the four sides of the load-bearing plate 20 13 , a plurality of vertical slots...
PUM
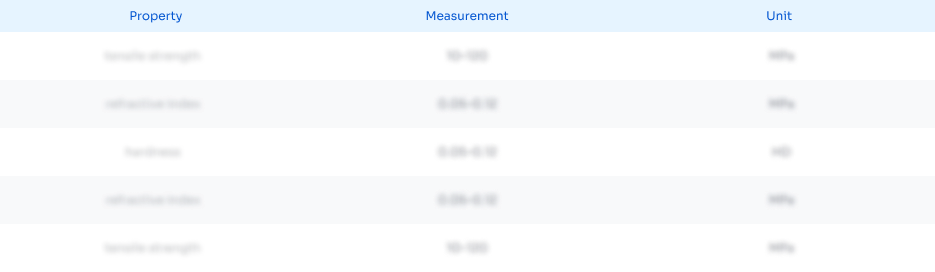
Abstract
Description
Claims
Application Information

- R&D Engineer
- R&D Manager
- IP Professional
- Industry Leading Data Capabilities
- Powerful AI technology
- Patent DNA Extraction
Browse by: Latest US Patents, China's latest patents, Technical Efficacy Thesaurus, Application Domain, Technology Topic, Popular Technical Reports.
© 2024 PatSnap. All rights reserved.Legal|Privacy policy|Modern Slavery Act Transparency Statement|Sitemap|About US| Contact US: help@patsnap.com