Temperature sensing drill point and self-adaptive control method used when planting robot prepares planting pit
A robot and drill needle technology, applied in the direction of adaptive control, temperature control, general control system, etc., can solve the problems of bone tissue necrosis, implant failure, and the temperature of bone tissue in the implant socket cannot be sensed and effectively controlled in real time. Safe and prevent bone damage
- Summary
- Abstract
- Description
- Claims
- Application Information
AI Technical Summary
Problems solved by technology
Method used
Image
Examples
Embodiment Construction
[0022] The present invention will be further described below in conjunction with the accompanying drawings.
[0023] refer to Figure 1 ~ Figure 3 , a temperature-sensing drill for implanting a planting nest by a planting robot, comprising a temperature-sensing drill body 1, one end of the body is a connecting portion 2, the other end of the body is a drill tip 3, and the body 1 is a hollow structure with a hollow interior It is divided into four areas, which are temperature sensitive area 11, moving area 12, reset area 13, signal generating area 14, and sealing and signal conducting area 15. The temperature sensitive area 11 is filled with temperature sensitive paraffin 111, and the moving area 12 places the piston 121, the reset area 13 places the return spring 131, the signal generating area 14 places the signal generator 144, and the sealing and signal conducting area 15 is filled with a sealing material 151 for sealing and placed for conducting Signal conducting sheet 15...
PUM
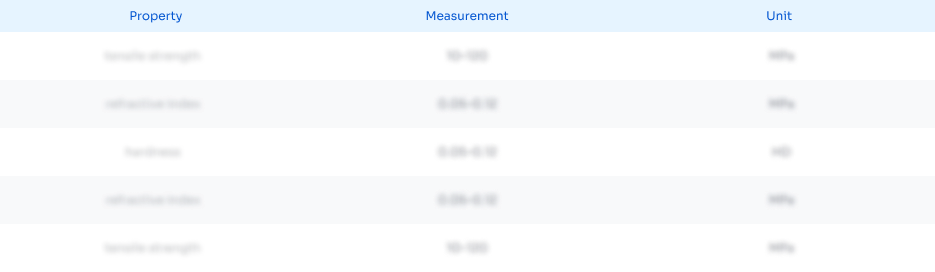
Abstract
Description
Claims
Application Information

- Generate Ideas
- Intellectual Property
- Life Sciences
- Materials
- Tech Scout
- Unparalleled Data Quality
- Higher Quality Content
- 60% Fewer Hallucinations
Browse by: Latest US Patents, China's latest patents, Technical Efficacy Thesaurus, Application Domain, Technology Topic, Popular Technical Reports.
© 2025 PatSnap. All rights reserved.Legal|Privacy policy|Modern Slavery Act Transparency Statement|Sitemap|About US| Contact US: help@patsnap.com