Pre-oxidization thermal coloring method for verdigris
A pre-oxidation and thermal coloring technology, applied in the coating process of metal materials, etc., can solve the problems of unnatural patina color, hard color, poor effect, etc., and achieve the effects of increasing service life, soft color, and improving production efficiency
- Summary
- Abstract
- Description
- Claims
- Application Information
AI Technical Summary
Problems solved by technology
Method used
Examples
Embodiment 1
[0031] A verdigris pre-oxidation thermal coloring method, comprising the following steps:
[0032] (1) Grinding the surface of the copper plate;
[0033] (2) use degreasing water to clean, and described degreasing water is made of following raw materials by weight: 9 parts of degreasing powder, 660 parts of water;
[0034] (3) Use water with activated carbon to clean the copper plate;
[0035] (4) Heating the copper plate to 160℃~260℃, then spraying the oxidizing syrup on the surface of the copper plate evenly for 5 times, and using the flame spray gun to continuously heat the copper plate for 1 hour to realize the patina coloring of the copper plate. The oxidizing syrup is made from the following raw materials in parts by weight : 8 parts of iron sulfate, 25 parts of copper sulfate, 1800 parts of water.
[0036] (5) After the copper plate is cooled, spray a layer of 20-25μm transparent fluorocarbon protective paint on its surface, and then place the copper plate in an oven ...
Embodiment 2
[0038] A verdigris pre-oxidation thermal coloring method, comprising the following steps:
[0039] (1) Grinding the surface of the copper plate;
[0040] (2) use degreasing water to clean, and described degreasing water is made of following raw materials by weight: 10 parts of degreasing powder, 700 parts of water;
[0041] (3) Use water with activated carbon to clean the copper plate;
[0042] (4) Heating the copper plate to 160℃~260℃, then evenly spraying the oxidizing syrup on the surface of the copper plate for 8 times, and using the flame spray gun to continuously heat the copper plate for 1.5h to realize the patina coloring of the copper plate. The oxidizing syrup is prepared from the following raw materials in parts by weight Composition: 10 parts of iron sulfate, 30 parts of copper sulfate, and 2000 parts of water.
[0043] (5) After the copper plate is cooled, spray a layer of 20-25μm transparent fluorocarbon protective paint on its surface, and then place the coppe...
Embodiment 3
[0045] A verdigris pre-oxidation thermal coloring method, comprising the following steps:
[0046] (1) Grinding the surface of the copper plate;
[0047] (2) adopt degreasing water to clean, and described degreasing water is made of following raw materials in parts by weight: 11 parts of degreasing powder, 720 parts of water;
[0048] (3) Use water with activated carbon to clean the copper plate;
[0049] (4) Heating the copper plate to 160℃~260℃, then spraying the oxidizing syrup on the surface of the copper plate evenly for 10 times, and using the flame spray gun to continuously heat the copper plate for 2 hours to realize the patina coloring of the copper plate. The oxidizing syrup is made from the following raw materials by weight : 12 parts of iron sulfate, 35 parts of copper sulfate, 2200 parts of water.
[0050] (5) After the copper plate is cooled, spray a layer of 20-25μm transparent fluorocarbon protective paint on its surface, and then place the copper plate in an...
PUM
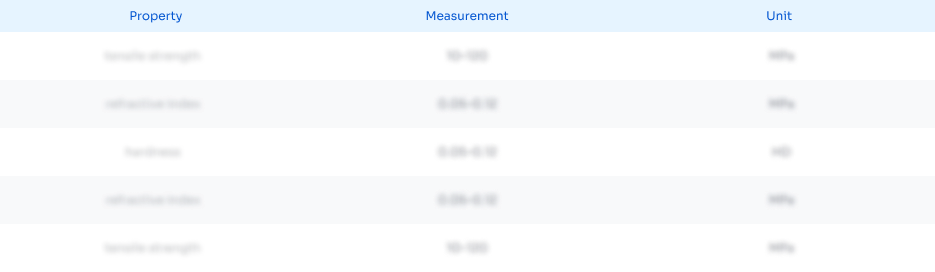
Abstract
Description
Claims
Application Information

- Generate Ideas
- Intellectual Property
- Life Sciences
- Materials
- Tech Scout
- Unparalleled Data Quality
- Higher Quality Content
- 60% Fewer Hallucinations
Browse by: Latest US Patents, China's latest patents, Technical Efficacy Thesaurus, Application Domain, Technology Topic, Popular Technical Reports.
© 2025 PatSnap. All rights reserved.Legal|Privacy policy|Modern Slavery Act Transparency Statement|Sitemap|About US| Contact US: help@patsnap.com