Resin vacuum forming device and component preparation method
A vacuum forming and resin technology, which is applied in the field of composite material forming devices, can solve the problems of poor component performance, poor air tightness and high porosity, and achieve the effects of reducing production costs, efficient preparation and simple operation.
- Summary
- Abstract
- Description
- Claims
- Application Information
AI Technical Summary
Problems solved by technology
Method used
Image
Examples
Embodiment Construction
[0027] The specific embodiments of the present invention will be described in detail below in conjunction with the accompanying drawings.
[0028] In one embodiment of the present invention, as Figure 1~4 As shown, a resin vacuum forming device is provided, including a curing device 1 and a mold 3, the mold 3 is arranged inside the curing device 1, and the mold 3 is sequentially provided with a vacuum bag 2, an air guiding tool, and a vacuum Bag one 13, the air guide tooling comprises U-shaped air guide bracket 14 and vacuum tank 5, vacuum tank 5 is arranged on the air guide bracket 14, one side of vacuum tank 5 is connected with vacuum bag one 13 by vacuum tube one 6, and vacuum tank 5 is other A pair of matching vacuum nozzles 7 are arranged on one side and the vacuum bag 2, and the vacuum nozzles 7 are connected to the vacuum system through the vacuum tube 2 8, and a matching single-permeable membrane 1 is arranged on the outside of the air guide bracket 14 and the vacuum ...
PUM
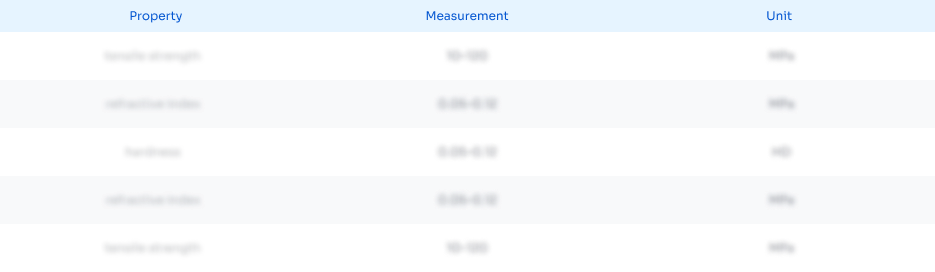
Abstract
Description
Claims
Application Information

- R&D
- Intellectual Property
- Life Sciences
- Materials
- Tech Scout
- Unparalleled Data Quality
- Higher Quality Content
- 60% Fewer Hallucinations
Browse by: Latest US Patents, China's latest patents, Technical Efficacy Thesaurus, Application Domain, Technology Topic, Popular Technical Reports.
© 2025 PatSnap. All rights reserved.Legal|Privacy policy|Modern Slavery Act Transparency Statement|Sitemap|About US| Contact US: help@patsnap.com