A method for forming a combined sand core
A molding method and sand core technology, applied in casting molding equipment, cores, molds, etc., can solve the problems of increasing the burden of printing head equipment, increasing the sand intake of the sand core, and increasing the strength of the molding sand, so as to improve the quality of castings. , strong forming ability, the effect of improving ability
- Summary
- Abstract
- Description
- Claims
- Application Information
AI Technical Summary
Problems solved by technology
Method used
Image
Examples
Embodiment Construction
[0021] In order to illustrate the technical solution of the present invention more clearly, the present invention will be further described in detail below in conjunction with specific examples. Please note that the embodiments described below are exemplary only for explaining the present invention, and should not be construed as limiting the present invention.
[0022] In this embodiment, a forming method of column castings, combining Figure 1-Figure 7 In detail, the casting result relationship is as figure 1 , there is a column guide rail 2 on the column casting 1, and the molding method includes the following steps:
[0023] Process design, use 3D design software to design the casting process, choose the pouring direction, design the important surface of the casting guide rail 2 on the lower box surface, set the product guide rail downward, and there are enough holes on the side of the pouring direction. Sand core; the pouring system uses bottom pouring pouring, which ca...
PUM
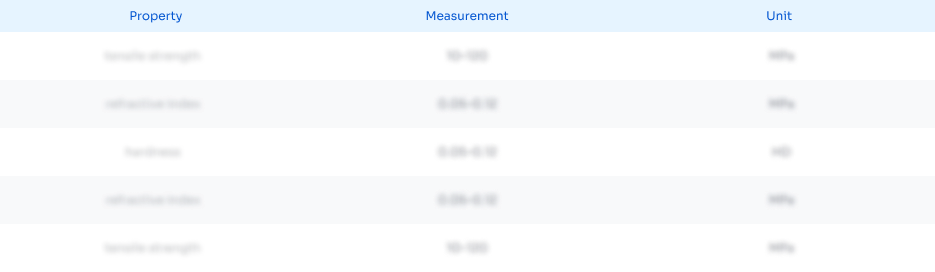
Abstract
Description
Claims
Application Information

- Generate Ideas
- Intellectual Property
- Life Sciences
- Materials
- Tech Scout
- Unparalleled Data Quality
- Higher Quality Content
- 60% Fewer Hallucinations
Browse by: Latest US Patents, China's latest patents, Technical Efficacy Thesaurus, Application Domain, Technology Topic, Popular Technical Reports.
© 2025 PatSnap. All rights reserved.Legal|Privacy policy|Modern Slavery Act Transparency Statement|Sitemap|About US| Contact US: help@patsnap.com