Implementation method for detaching TBM in tunnel
An implementation method and technology of content, applied in the field of dismantling TBM in the hole, can solve the problems of small contact surface, damage of track and cable tray frame, poor stability, etc.
- Summary
- Abstract
- Description
- Claims
- Application Information
AI Technical Summary
Problems solved by technology
Method used
Image
Examples
Embodiment approach
[0025] Such as figure 1 , figure 2 and image 3 As shown, the implementation method of disassembling the TBM in the hole involved in the present invention includes the following contents:
[0026] Arrange the dismantling chamber;
[0027] After the TBM excavation is completed, separate the TBM shield body and the rear support from the traction cylinder, and then slide to the dismantling chamber respectively;
[0028] Shield taxiing: Lay track I, introduce power and cooling water, transform the hydraulic pump station of the advanced drilling system, and connect with the high-pressure oil pipe of the oil cylinder at the inner bottom of the tail shield to complete the propulsion of the TBM shield on the track;
[0029] Back supporting sliding: the connection structure between the trolleys of the supporting sliding system after disassembly, each trolley includes road wheels, lower wheel frames and upper wheel frames. On the upper part of the lower wheel frame, newly install t...
PUM
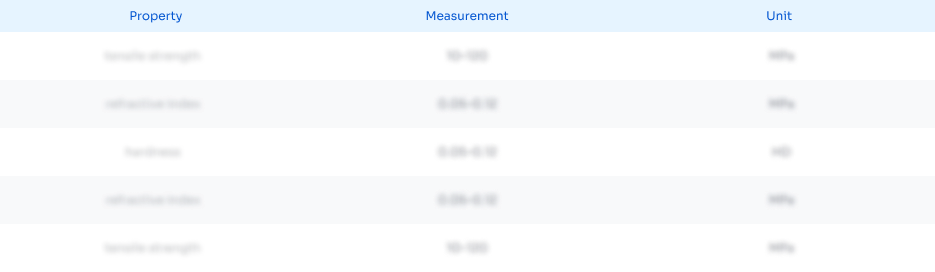
Abstract
Description
Claims
Application Information

- R&D
- Intellectual Property
- Life Sciences
- Materials
- Tech Scout
- Unparalleled Data Quality
- Higher Quality Content
- 60% Fewer Hallucinations
Browse by: Latest US Patents, China's latest patents, Technical Efficacy Thesaurus, Application Domain, Technology Topic, Popular Technical Reports.
© 2025 PatSnap. All rights reserved.Legal|Privacy policy|Modern Slavery Act Transparency Statement|Sitemap|About US| Contact US: help@patsnap.com