Fault-tolerant control system and method for four-direct-current motor series system
A DC motor, fault-tolerant control technology, applied in the control system, motor speed or torque control, multiple motor speed adjustment, etc., can solve the problems of failure diagnosis, large torque ripple, and low work efficiency
- Summary
- Abstract
- Description
- Claims
- Application Information
AI Technical Summary
Problems solved by technology
Method used
Image
Examples
Embodiment
[0089] This embodiment provides a fault-tolerant control system for a series system of four DC motors. The power supply is powered by a DC voltage source. The first DC motor DCM1, the second DC motor DCM2, the third DC motor DCM3 and the fourth DC motor DCM4 adopt Five inverter working bridge arms are driven, and five inverter working bridge arms include ten switch inverter drives; each inverter working bridge arm includes two power MOS switch tubes and fuses connected in series , the upper bridge arm T in the working bridge arm of the first inverter 1 and the first fuse F 1 connection, the upper bridge arm T in the working bridge arm of the second inverter 3 and a third fuse F 3 connection, the upper bridge arm T in the working bridge arm of the third inverter 5 and the fifth fuse F 5 connection, the upper bridge arm T in the working bridge arm of the fourth inverter 7 and the seventh fuse F 7 connection, the upper bridge arm T of the fifth inverter working bridge arm ...
PUM
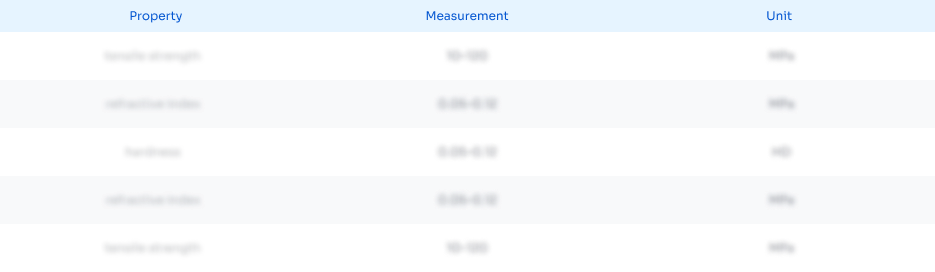
Abstract
Description
Claims
Application Information

- Generate Ideas
- Intellectual Property
- Life Sciences
- Materials
- Tech Scout
- Unparalleled Data Quality
- Higher Quality Content
- 60% Fewer Hallucinations
Browse by: Latest US Patents, China's latest patents, Technical Efficacy Thesaurus, Application Domain, Technology Topic, Popular Technical Reports.
© 2025 PatSnap. All rights reserved.Legal|Privacy policy|Modern Slavery Act Transparency Statement|Sitemap|About US| Contact US: help@patsnap.com