Production method of fatty alcohol-polyoxyethylene ether
A technology of alcohol polyoxyethylene ether and production method, which is applied in the preparation of ether from alkylene oxide, chemical instruments and methods, preparation of ether, etc., and can solve the problems of low content of volatile organic compounds and high content of volatile organic compounds
- Summary
- Abstract
- Description
- Claims
- Application Information
AI Technical Summary
Problems solved by technology
Method used
Image
Examples
Embodiment 1
[0057] Put 100g of dodecanol, 0.5g of potassium hydroxide, and 0.5g of sodium borohydride into a stirred 1-liter high-pressure reactor, seal the high-pressure reactor, start stirring, and replace nitrogen three times. Pressure evacuation and dehydration for 30 minutes, then feed ethylene oxide into the reactor, control the reaction temperature at 145°C and the reaction pressure at 0.20MPa, until the total amount of fed ethylene oxide is 213g, stop feeding ethylene oxide , and then maintain the reaction temperature until the pressure of the reactor no longer drops, indicating that the aging reaction is completed, the temperature is lowered to 100 ° C, -0.096 MPa vacuum for 10 minutes, the temperature is cooled to 75 ° C, and the pH is neutralized to 7.5 with acetic acid to obtain twelve Alcohol polyoxyethylene (9) ether products.
[0058] The residual amount of volatile organic compounds in the lauryl alcohol polyoxyethylene (9) ether product was measured to be 14.6 mg kg -1 ....
Embodiment 2
[0060] Put 100g of dodecyl alcohol, 0.5g of potassium hydroxide, and 0.5g of tri-sec-butyl sodium borohydride into a stirred 1-liter high-pressure reactor, seal the high-pressure reactor, start stirring, and replace nitrogen three times, at a temperature of 100°C and The pressure of -0.096MPa was evacuated and dehydrated for 30 minutes, and then ethylene oxide was passed into the reactor, and the reaction temperature was controlled at 145°C and the reaction pressure was 0.20MPa until the total amount of ethylene oxide was 213g, and then stopped. Ethylene oxide, then maintain the reaction temperature until the pressure of the reactor no longer drops, indicating that the aging reaction is completed, lower the temperature to 100°C, vacuumize at -0.096MPa for 10 minutes, cool the temperature to 75°C, and neutralize the pH to 7.5 with acetic acid , to obtain polyoxyethylene lauryl alcohol (9) ether product.
[0061] The residual amount of volatile organic compounds in the lauryl al...
Embodiment 3
[0063] Put 100g of dodecyl alcohol, 0.5g of potassium hydroxide, and 0.5g of disodium stannous citrate into a stirred 1-liter high-pressure reactor, seal the high-pressure reactor, start stirring, and replace nitrogen three times, at a temperature of 100°C and - The pressure of 0.096MPa was evacuated and dehydrated for 30 minutes, then ethylene oxide was passed into the reactor, the controlled reaction temperature was 145°C and the reaction pressure was 0.20MPa, until the total amount of ethylene oxide passed into was 213g, and the loop was stopped. Oxyethane, then maintain the reaction temperature until the pressure of the reactor no longer drops, indicating that the aging reaction is completed, lower the temperature to 100°C, vacuumize at -0.096MPa for 10 minutes, cool the temperature to 75°C, and neutralize with acetic acid to a pH of 7.5. Obtain lauryl alcohol polyoxyethylene (9) ether product.
[0064] The residual amount of volatile organic compounds in the lauryl alcoho...
PUM
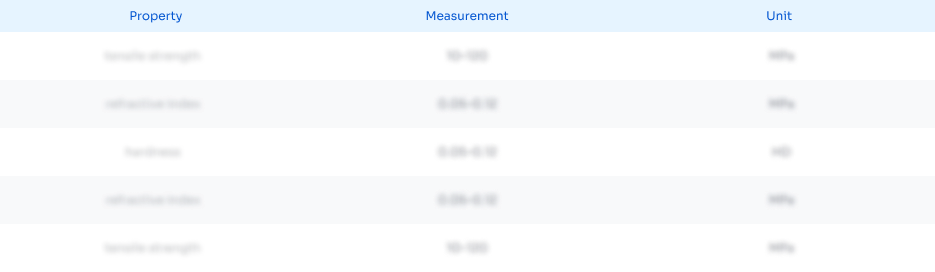
Abstract
Description
Claims
Application Information

- Generate Ideas
- Intellectual Property
- Life Sciences
- Materials
- Tech Scout
- Unparalleled Data Quality
- Higher Quality Content
- 60% Fewer Hallucinations
Browse by: Latest US Patents, China's latest patents, Technical Efficacy Thesaurus, Application Domain, Technology Topic, Popular Technical Reports.
© 2025 PatSnap. All rights reserved.Legal|Privacy policy|Modern Slavery Act Transparency Statement|Sitemap|About US| Contact US: help@patsnap.com