Rotation assembly
A technology of rotating components and rotating angles, applied in the field of aircraft, can solve problems such as difficulty in maintaining the unfolded or folded state, inaccurate rotating angles, damage, etc., to ensure flight stability and safety, ensure stability, and ensure compactness Effect
- Summary
- Abstract
- Description
- Claims
- Application Information
AI Technical Summary
Problems solved by technology
Method used
Image
Examples
Embodiment 1
[0027] Such as Figure 1 to Figure 5 As shown, an aircraft mainly includes a fuselage a, an arm assembly b, and a rotor power assembly c. The fuselage a includes a shell 1 formed of a plate-shaped material with a containing cavity inside, and the shell The body 1 is provided with a cavity 11 recessed in the wall surface, the arm assembly b is hinged to the cavity 11 to form a folding arm structure, the rotor power assembly c is arranged on the arm assembly b, and the A foldable landing gear d is also provided on the arm assembly b;
[0028] The shell 1, the arm assembly b is specifically processed and formed by carbon fiber composite material. The carbon fiber composite material has excellent mechanical properties, its specific gravity is small, the rigidity is high, the strength is high, and the comprehensive indicators of specific strength and specific modulus are high, so as to protect the shell 1, The arm assembly b has excellent structural strength, so that the fuselage a a...
Embodiment 2
[0042] Such as Image 6 As shown, the rotating assembly 3 mainly includes a rotating angle piece 31, an angle positioning piece 32 that rotates relative to the rotating angle piece 31, and an articulated locking mechanism that operates between a locked position and an unlocked position. The rotating angle piece 31, an angle positioning piece 32 is connected to the two parts that need to be hinged separately. In this embodiment, the turning angle piece 31 is fixed to the folding arm b2, and the angle positioning piece 32 is fixed to the main arm b1, so that the folding arm b2 is fixed to the main arm b1. They can be rotated relative to each other through the connection of the rotating assembly 3. The rotating angle member 31 is provided with two sets of engaging portions 311 at intervals in the rotating circumferential direction, one of which is the angle position in the collapsed state, and the other is the unfolded state. The angle positioning member 32 is provided with a posit...
Embodiment 3
[0045] Such as Figure 7 As shown, the rotating assembly 3 mainly includes a rotating angle piece 31, an angle positioning piece 32 that rotates relative to the rotating angle piece 31, and an articulated locking mechanism that operates between a locked position and an unlocked position. The rotating angle piece 31, an angle positioning piece 32 is respectively connected with the two parts that need to be hinged. The rotation angle member 31 is provided with two sets of engaging parts 311 at intervals in the rotation circumferential direction, one of which is the angle position in the collapsed state, and the other is in the unfolded state. The angle positioning member 32 is provided with a positioning portion 321 that cooperates with the engaging portion 311. When the rotation angle member 31 and the angle positioning member 32 rotate relative to each other, the positioning portion 321 engages with different angular positions When the part 311 is matched, the rotation angle pos...
PUM
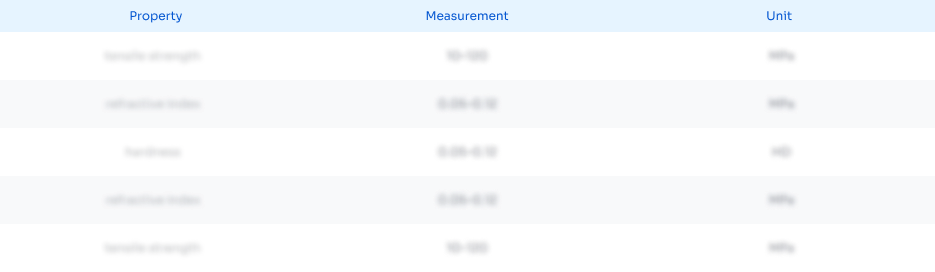
Abstract
Description
Claims
Application Information

- Generate Ideas
- Intellectual Property
- Life Sciences
- Materials
- Tech Scout
- Unparalleled Data Quality
- Higher Quality Content
- 60% Fewer Hallucinations
Browse by: Latest US Patents, China's latest patents, Technical Efficacy Thesaurus, Application Domain, Technology Topic, Popular Technical Reports.
© 2025 PatSnap. All rights reserved.Legal|Privacy policy|Modern Slavery Act Transparency Statement|Sitemap|About US| Contact US: help@patsnap.com