Optimal design method of variable-rigidity spiral spring
A coil spring and optimized design technology, applied in the field of coil springs, can solve the problem that coil springs cannot meet the load capacity, compression and extension stroke and layout space at the same time, meet the needs of use, ensure driving stability and safety, and simplify processing. The effect of craftsmanship
- Summary
- Abstract
- Description
- Claims
- Application Information
AI Technical Summary
Problems solved by technology
Method used
Image
Examples
specific Embodiment approach
[0031] Such as Figure 1 to Figure 3 Shown is a specific embodiment of an optimal design method for a variable stiffness helical spring of the present invention, comprising the following steps:
[0032] 1. Estimate the initial value of the wire diameter, initial pitch, inner diameter and length of the coil spring according to the required load and compression and extension stroke of the coil spring.
[0033] 2. Input the initial value of wire diameter, initial value of pitch, initial value of inner diameter and initial value of length of the coil spring into the simulation platform, and establish the finite element model of the coil spring.
[0034] 3. Use the finite element analysis method in the simulation platform to analyze the structural stress of the coil spring finite element model to determine its stress level and dangerous point location.
[0035] 4. According to the stress level and dangerous point position of the coil spring finite element model, optimize the wire ...
PUM
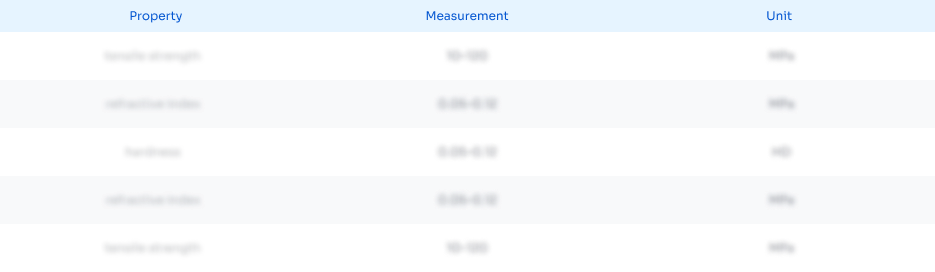
Abstract
Description
Claims
Application Information

- R&D Engineer
- R&D Manager
- IP Professional
- Industry Leading Data Capabilities
- Powerful AI technology
- Patent DNA Extraction
Browse by: Latest US Patents, China's latest patents, Technical Efficacy Thesaurus, Application Domain, Technology Topic, Popular Technical Reports.
© 2024 PatSnap. All rights reserved.Legal|Privacy policy|Modern Slavery Act Transparency Statement|Sitemap|About US| Contact US: help@patsnap.com