Hydraulic valve with valve element friction compensation function under centrifugal environment
A hydraulic valve and friction technology, applied in the field of hydraulic valves, can solve the problems of increasing the dead zone range, reducing the motion performance, slowing down the response speed, etc. effect of time
- Summary
- Abstract
- Description
- Claims
- Application Information
AI Technical Summary
Problems solved by technology
Method used
Image
Examples
Embodiment 1
[0028] A hydraulic valve with spool friction compensation in a centrifugal environment, such as Figure 1~Figure 6 As shown, it includes valve body 201, main spool 202, reversing spool 204 and compensating spool 401, as figure 2 As shown, the valve body 201 is provided with a main cavity 104, a reversing cavity and a control cavity, and the main valve core 202 is slidably arranged in the main cavity 104; the left and right side walls of the reversing cavity are respectively provided with Return spring 218, reversing valve core 204 is slidably installed between two return springs 218, reversing valve core 204 is provided with reversing protrusion 220, and the outside of reversing protrusion 220 is provided with pressure cavity 213, and reversing protrusion 220 is close to and blocks the inner end of the pressure chamber 213, the length of the outer side of the reversing protrusion 220 is slightly longer than the length of the inner end of the pressure chamber 213, and the reve...
Embodiment 2
[0034] The difference from Embodiment 1 is that it also includes a pilot valve 602, such as figure 2 As shown, the reversing valve core 204 divides the reversing cavity into a left end cavity 217A and a right end cavity 217B. The left and right sides of the main valve core 202 are respectively provided with annular protrusions 219, and the annular protrusions 219 separate the main cavity. 104 is divided into a left cavity 208 and a right cavity 209, the left cavity 208 communicates with the left end cavity 217A through a flow channel, and the right cavity 209 communicates with the right end cavity 217B through a flow channel, as Figure 5 As shown, the left cavity 208 and the right cavity 209 communicate with different control ports of the pilot valve respectively, and the control port of the pilot valve 602 includes the first connection port P of the pilot valve. A3 and the second port of the pilot valve P B3 . The pilot valve 602 is used to assist in controlling the main ...
PUM
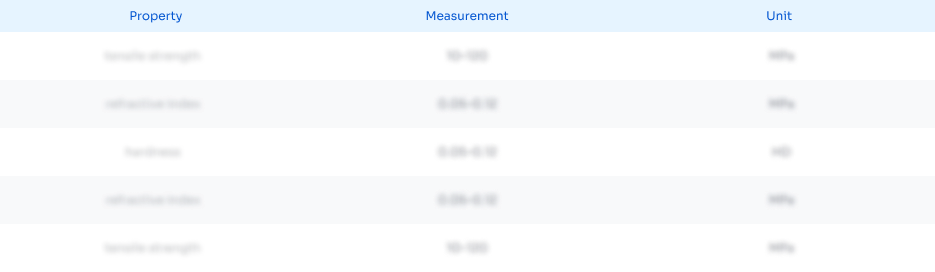
Abstract
Description
Claims
Application Information

- R&D Engineer
- R&D Manager
- IP Professional
- Industry Leading Data Capabilities
- Powerful AI technology
- Patent DNA Extraction
Browse by: Latest US Patents, China's latest patents, Technical Efficacy Thesaurus, Application Domain, Technology Topic, Popular Technical Reports.
© 2024 PatSnap. All rights reserved.Legal|Privacy policy|Modern Slavery Act Transparency Statement|Sitemap|About US| Contact US: help@patsnap.com