Low Frequency Inductive Magnetic Sensor Based on Nonvolatile Tuning
A magnetic sensor and inductive technology, used in instruments, measuring magnetic variables, measuring devices, etc., can solve the problems of magnetic loss of soft magnetic materials, increase the cost of current sources, limit wide application, etc., to achieve non-volatile tuning, improve Effective magnetic permeability, the effect of enhancing the convergence ability
- Summary
- Abstract
- Description
- Claims
- Application Information
AI Technical Summary
Problems solved by technology
Method used
Image
Examples
Embodiment Construction
[0020] The present invention will be further described below in conjunction with the accompanying drawings and examples, but the protection scope of the present invention should not be limited thereto.
[0021] according to figure 1 with figure 2 , as can be seen from the figure, the present invention is based on a non-volatile tuned low-frequency inductive magnetic sensor, including a sensing unit structure and an adjustable capacitance 6 driven by a piezoelectric beam, and the sensing unit structure is on the substrate 8 From bottom to top, giant magnetostrictive layer 5, multi-layer stepped soft magnetic film 1, insulating layer 7, integrated planar excitation coil 2 and planar induction coil 3, insulating layer 7, multi-layer stepped soft magnetic film 1 , piezoelectric transformer layer 4; the integrated planar excitation coil 2 and planar induction coil 3, insulating layer 7, and multi-layer stepped soft magnetic film 1 form a sandwich structure, and the adjustable cap...
PUM
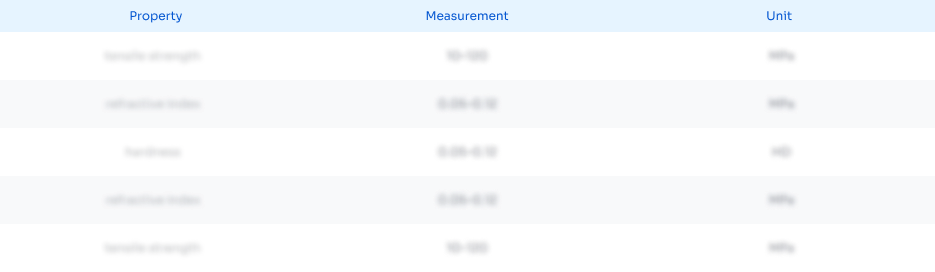
Abstract
Description
Claims
Application Information

- R&D
- Intellectual Property
- Life Sciences
- Materials
- Tech Scout
- Unparalleled Data Quality
- Higher Quality Content
- 60% Fewer Hallucinations
Browse by: Latest US Patents, China's latest patents, Technical Efficacy Thesaurus, Application Domain, Technology Topic, Popular Technical Reports.
© 2025 PatSnap. All rights reserved.Legal|Privacy policy|Modern Slavery Act Transparency Statement|Sitemap|About US| Contact US: help@patsnap.com