Processing method for improving flow precision of oil injecting ring
A processing method and technology of circulating flow, applied in the field of mechanical processing, can solve the problems of too large a single aperture grinding, can not meet the design requirements, and cannot be remedied when the flow exceeds the standard, so as to improve consistency and quality, and ensure timely and on-demand. The effect of delivering, reducing the number of traffic trials
- Summary
- Abstract
- Description
- Claims
- Application Information
AI Technical Summary
Problems solved by technology
Method used
Image
Examples
Embodiment Construction
[0035] The present invention will be described in detail below in conjunction with the accompanying drawings.
[0036] refer to figure 1 with figure 2 , a processing method for improving the flow accuracy of an injection ring, comprising the following steps:
[0037] Step 1, using the drilling and reaming process to process the oil injection hole and the oil inlet hole 1 of one oil circuit, the oil injection hole of one oil circuit includes the first oil injection hole 2 and the second oil injection hole 3, Carry out a single oil channel flow process test to determine the diameter of an oil inlet hole 1 when the oil injection holes include the first oil injection hole 2 and the second oil injection hole 3 and meet the median flow rate requirements under the machining accuracy level of the reaming process Φ 1 , the diameter Φ of the first injection hole 2 2 And the diameter Φ of the second fuel injection hole 3 3 ;
PUM
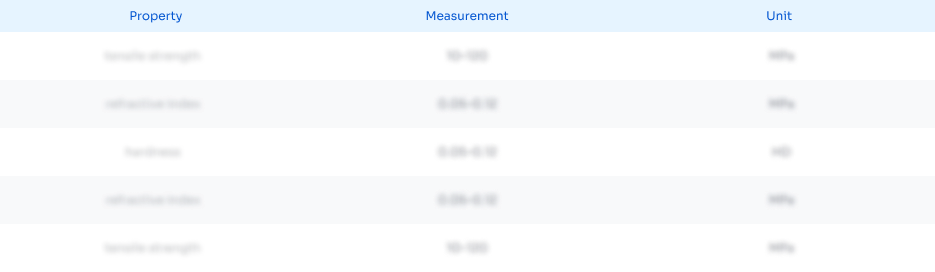
Abstract
Description
Claims
Application Information

- R&D Engineer
- R&D Manager
- IP Professional
- Industry Leading Data Capabilities
- Powerful AI technology
- Patent DNA Extraction
Browse by: Latest US Patents, China's latest patents, Technical Efficacy Thesaurus, Application Domain, Technology Topic, Popular Technical Reports.
© 2024 PatSnap. All rights reserved.Legal|Privacy policy|Modern Slavery Act Transparency Statement|Sitemap|About US| Contact US: help@patsnap.com