An intelligent fault diagnosis method for rotating machinery under time-varying speed
A technology for rotating machinery and fault diagnosis, which is applied in the testing of mechanical components, testing of machine/structural components, instruments, etc. It can solve problems such as fault diagnosis that cannot be solved by deep learning methods, and achieve the effect of improving generalization ability
- Summary
- Abstract
- Description
- Claims
- Application Information
AI Technical Summary
Problems solved by technology
Method used
Image
Examples
Embodiment Construction
[0076] The present invention will be further described below in conjunction with the accompanying drawings.
[0077] Such as figure 1 As shown, the intelligent fault diagnosis method for rotating machinery under time-varying speed combines keyless phase order tracking with deep learning methods to realize self-adaptive intelligent fault diagnosis and identification of rotating machinery under variable speed conditions, which specifically includes the following steps:
[0078] Step 1: Use the acceleration sensor to collect the vibration signal of the bearing;
[0079] Step 2: Perform Gabor expansion on the collected signal to obtain a Gabor time-frequency diagram;
[0080] Step 3: Select an obvious order component in the Gabor time-frequency diagram, place control points on its ridge line, connect the control points with a straight line, obtain the filter center frequency line by linear interpolation, and calculate the filter neighborhood;
[0081] Step 4: Obtain the Gabor co...
PUM
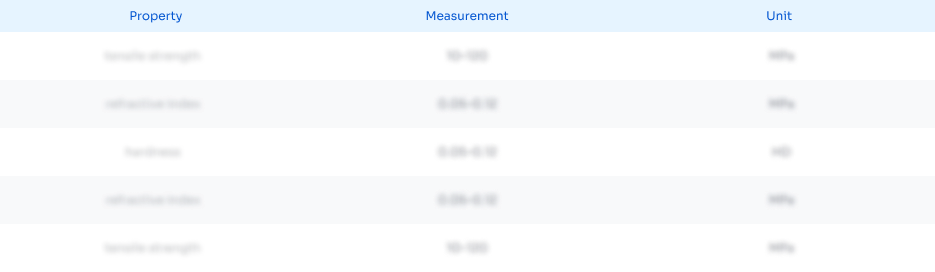
Abstract
Description
Claims
Application Information

- R&D
- Intellectual Property
- Life Sciences
- Materials
- Tech Scout
- Unparalleled Data Quality
- Higher Quality Content
- 60% Fewer Hallucinations
Browse by: Latest US Patents, China's latest patents, Technical Efficacy Thesaurus, Application Domain, Technology Topic, Popular Technical Reports.
© 2025 PatSnap. All rights reserved.Legal|Privacy policy|Modern Slavery Act Transparency Statement|Sitemap|About US| Contact US: help@patsnap.com