A method for extracting vanadium by multi-stage roasting of stone coal vanadium ore and enhanced acid-mixing aging
A technology for stone coal mine and stone coal vanadium, which is applied in the field of multi-stage roasting and strengthening of acid mixing and ripening for vanadium extraction in stone coal and vanadium mine, can solve problems such as safety, environment, problems, etc., and achieves improvement of oxidation rate and leaching rate, simple process and effect. good effect
- Summary
- Abstract
- Description
- Claims
- Application Information
AI Technical Summary
Problems solved by technology
Method used
Image
Examples
Embodiment 1
[0041] Process such as figure 1 shown;
[0042] Stone coal vanadium ore block contains V by mass percentage 2 o 5 0.9~1.3%, K2 O, Al 2 o 3 , CaO, TiO 2 ,P 2 o 5 The mass percentages of C and C are 3.54%, 12.58%, 3.37%, 1.23%, 0.67% and 15.75% respectively; the stone coal vanadium ore block with a particle size of 10-200mm is crushed to 2-10mm to make stone coal ore particles; Grinding the stone coal ore particles to a mass content of -0.074mm of 65% to make stone coal ore powder;
[0043] A suspension roasting device with a combustion station at the bottom and an induced draft fan connected to the top is adopted. When the induced draft fan is turned on, air and gas are introduced into the combustion station for combustion to generate hot flue gas, which then enters the suspension roasting device; at the same time, the stone The coal ore powder is transported to the suspension roasting device, and the stone coal ore powder enters from the upper part of the suspension r...
Embodiment 2
[0049] Method is with embodiment 1, and difference is:
[0050] (1) Stone coal vanadium ore block contains V by mass percentage 2 o 5 0.93%, Al 2 o 3 The mass percentages of CaO, C and C are 11.32%, 4.43% and 10.15% respectively; the mass content of stone coal ore particles ground to -0.074mm is 75%;
[0051] (2) Stone coal powder is roasted at 750°C with heat storage, and the residence time in the suspension roasting device is 50s;
[0052] (3) Decarburization and roasting at a temperature of 600 ° C, and the residence time of the heat storage stone coal ore powder in the decarburization roasting device is 20 minutes;
[0053] (4) The volume ratio of air and nitrogen in the mixed gas is 3; the temperature of the decarburized material is controlled at 800°C, and the residence time of the decarburized material in the crystal breaking roasting device is 60min;
[0054] (5) Add water and sulfuric acid solution to the crystal-breaking roasting material and stir and mix evenl...
Embodiment 3
[0057] Method is with embodiment 1, and difference is:
[0058] (1) The mass content of the part of stone coal mine particles ground to -0.038mm is 90%;
[0059] (2) Stone coal powder is roasted at 800°C with heat storage, and the residence time in the suspension roasting device is 30s;
[0060] (3) Decarburization and roasting at a temperature of 700 ° C, and the residence time of the heat storage stone coal ore powder in the decarburization roasting device is 15 minutes;
[0061] (4) The volume ratio of air and nitrogen in the mixed gas is 3.5; the temperature of the decarburized material is controlled at 850°C, and the residence time of the decarburized material in the crystal breaking roasting device is 50min;
[0062] (5) Add water and sulfuric acid solution to the crystal breaking and roasting material and stir and mix evenly, water accounts for 10% of the total mass of all materials, and sulfuric acid solution accounts for 35% of the total mass of all materials; 160 ° ...
PUM
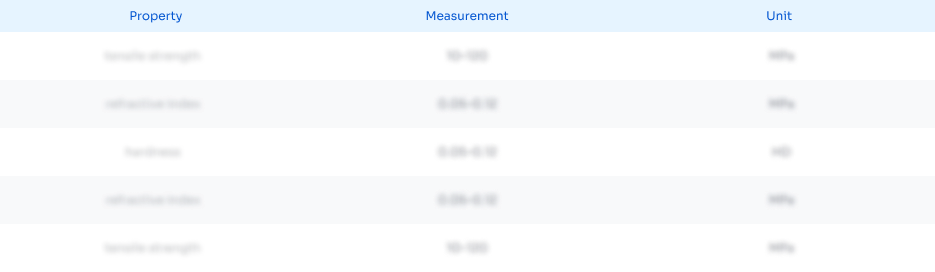
Abstract
Description
Claims
Application Information

- R&D
- Intellectual Property
- Life Sciences
- Materials
- Tech Scout
- Unparalleled Data Quality
- Higher Quality Content
- 60% Fewer Hallucinations
Browse by: Latest US Patents, China's latest patents, Technical Efficacy Thesaurus, Application Domain, Technology Topic, Popular Technical Reports.
© 2025 PatSnap. All rights reserved.Legal|Privacy policy|Modern Slavery Act Transparency Statement|Sitemap|About US| Contact US: help@patsnap.com