Micro-clamping robot
A robot and micro-clamping technology, applied in the direction of micro-manipulators, chucks, manipulators, etc., can solve the problem that the jaws no longer move in parallel
- Summary
- Abstract
- Description
- Claims
- Application Information
AI Technical Summary
Problems solved by technology
Method used
Image
Examples
Embodiment 1
[0076] Such as figure 1 The shown micro clamping robot that can realize six-degree-of-freedom space movement, the robot is realized by a precision electric table 3 that can move linearly along the X-axis, Y-axis and Z-axis to achieve three freedoms along the X-axis, Y-axis and Z-axis respectively. The two-axis precision electric rotary table 4 that can rotate along the X axis and the Z axis realizes the rotary motion along the X axis and the Z axis respectively, and the precision electric rotary table 5 that can rotate along the Y axis realizes the rotary motion along the Y axis. The rotational movement of the shaft; the clamping and releasing of tiny devices is realized by using the micro-clamp that integrates the jaw displacement sensing unit, the clamping force sensing unit and the micro-assembly force sensing unit at the same time. The micro gripper is installed on the micro gripper and precision positioning system adapter 7 through the base 8 . And the precision electric...
Embodiment 2
[0083] Such as figure 2 Shown is a three-degree-of-freedom micro-clamping robot consisting of a precision electric platform 3 that can move linearly along the X-axis, Y-axis, and Z-axis. The robot can move linearly along the X-axis, Y-axis, and Z-axis The precision electric platform 3 realizes the linear motion along the X-axis, Y-axis and Z-axis, and realizes the micro-gripper which integrates the jaw displacement sensing unit, the clamping force sensing unit and the micro-assembly force sensing unit at the same time. clamping and releasing. The clamping process of the tiny parts performed by the micro grippers is consistent with the process of Example 1.
[0084] It is also possible to change the structure of the micro-clamping robot by processing different structures of the jaw displacement, clamping force and micro-assembly force sensing mechanism on the micro-clamp single-piece compliant mechanism, and the specific implementation process is consistent with Example 1 . ...
Embodiment 3
[0086] Such as image 3Shown is a four-degree-of-freedom micro-clamping robot consisting of a precision electric platform 3 that can move linearly along the X-axis, Y-axis, and Z-axis, and a precision electric rotary table that can rotate along the Y-axis. The precision electric platform 3 that moves linearly along the X-axis, Y-axis and Z-axis realizes the linear movement along the X-axis, Y-axis and Z-axis, and the precision electric rotary table that can rotate along the Y-axis realizes the rotational movement along the Y-axis. The micro gripper integrating jaw displacement sensing unit, clamping force sensing unit and micro-assembly force sensing unit realizes the clamping and releasing of tiny parts. The clamping process of the tiny parts performed by the micro gripper is consistent with the clamping process in Example 1.
[0087] It is also possible to change the structure of the micro-clamping robot by processing different structures of jaw displacement, clamping force...
PUM
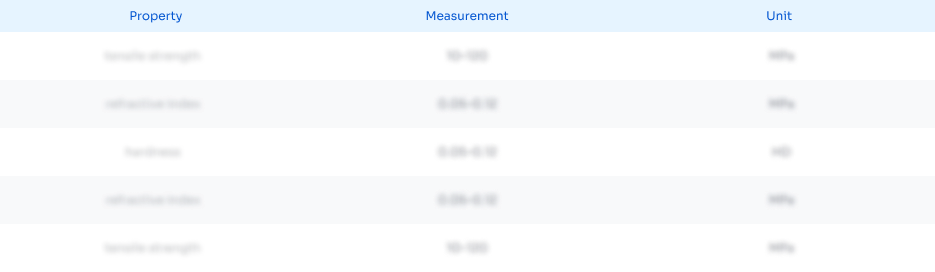
Abstract
Description
Claims
Application Information

- R&D
- Intellectual Property
- Life Sciences
- Materials
- Tech Scout
- Unparalleled Data Quality
- Higher Quality Content
- 60% Fewer Hallucinations
Browse by: Latest US Patents, China's latest patents, Technical Efficacy Thesaurus, Application Domain, Technology Topic, Popular Technical Reports.
© 2025 PatSnap. All rights reserved.Legal|Privacy policy|Modern Slavery Act Transparency Statement|Sitemap|About US| Contact US: help@patsnap.com