MEMS gyroscope online frequency difference identification method based on noise power spectrum estimation
A technology of noise power spectrum and identification method, which is applied in the field of online frequency difference identification of MEMS gyroscopes based on noise power spectrum estimation, and can solve problems such as high repeatability requirements, poor real-time performance, and affecting the normal working state of gyroscopes
- Summary
- Abstract
- Description
- Claims
- Application Information
AI Technical Summary
Problems solved by technology
Method used
Image
Examples
Embodiment Construction
[0055] like figure 2 As shown, a MEMS gyroscope online frequency difference identification method based on noise power spectrum estimation includes the following steps:
[0056] (1) According to the Q value of the detected mode and the preset resonance frequency f y0 , determine the power spectrum theoretical curve N(f) of the mechanical thermal noise of the gyroscope resonator at the output end of the detection mode, and use this as a benchmark for comparing and finding the resonance frequency of the detection mode;
[0057] (2) When the gyroscope is working normally, the Coriolis force, the orthogonal force and the mechanical thermal noise of the resonant oscillator act on the detection mode of the gyroscope at the same time, and form a voltage response at the output end of the detection mode; Perform voltage sampling and Fourier analysis to obtain the power spectrum curve M(f) of the output signal;
[0058] (3) Cross-correlate the theoretical power spectrum curve N(f) wi...
PUM
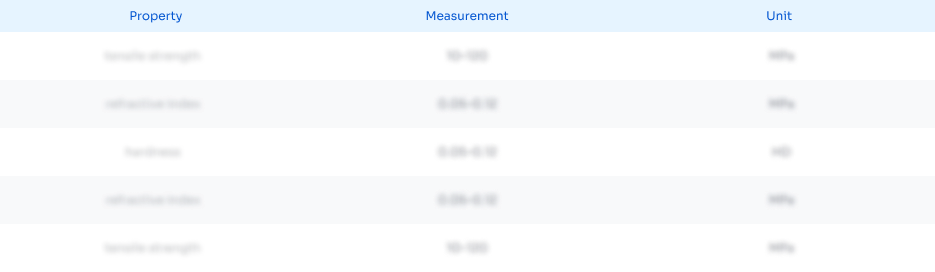
Abstract
Description
Claims
Application Information

- R&D
- Intellectual Property
- Life Sciences
- Materials
- Tech Scout
- Unparalleled Data Quality
- Higher Quality Content
- 60% Fewer Hallucinations
Browse by: Latest US Patents, China's latest patents, Technical Efficacy Thesaurus, Application Domain, Technology Topic, Popular Technical Reports.
© 2025 PatSnap. All rights reserved.Legal|Privacy policy|Modern Slavery Act Transparency Statement|Sitemap|About US| Contact US: help@patsnap.com