Moving bed reaction furnace for producing sponge iron by direct reduction of gas base
A technology of sponge iron and reaction furnace, which is applied in the direction of hearth furnace, furnace, furnace type, etc., can solve the problems of high dust content, coking and clogging of solid materials, etc., to reduce dust content, prevent coking and clogging, and avoid bed The effect of sintering
- Summary
- Abstract
- Description
- Claims
- Application Information
AI Technical Summary
Problems solved by technology
Method used
Image
Examples
Embodiment 1
[0036] A moving bed reactor for the production of sponge iron by gas-based direct reduction, the structure of which is as follows figure 1 As shown, the whole is a vertical cylindrical structure, which consists of the upper slightly enlarged head section 1, the middle cylinder section 2 and the lower cone section 3 connected in sequence from top to bottom. The specific structure and function of each part are as follows:
[0037]The upper part of the micro-enlarging head section 1 is provided with an exhaust gas outlet 12 for discharging reaction exhaust gas; the top is provided with a solid material uniform distribution chute 11, and solid materials such as iron oxide pellets enter the reaction furnace along the solid material uniform distribution chute 11. The reduction reaction is carried out in the reaction furnace, preferably 4 to 12 solid material uniform distribution chute 11, more preferably 6, to ensure that the charge is more evenly distributed in the furnace body; the...
Embodiment 2
[0042] A moving bed reaction furnace for gas-based direct reduction to produce sponge iron, which is a further refinement of some options in Example 1, and is used for gas-based direct reduction to produce sponge iron in a moving bed reaction furnace for processing iron oxide pellets , the furnace body design of the moving bed reactor and the reaction process in it are:
[0043] The shell of the reaction furnace is made of GH474 high-temperature steel, and the interior is coated with a composite high-temperature resistant coating mainly composed of corundum. The iron oxide pellets are fed into the reaction furnace from the micro-expansion head section 1 top of the reaction furnace, and the reduction reaction is completed in the reaction furnace. The number of solid material uniform distribution pipes 11 is 6.
[0044] The high-temperature reducing gas enters the gas distributor 22 from the reducing gas inlet 21 of the cylinder section 2 in the middle of the reaction furnace, a...
PUM
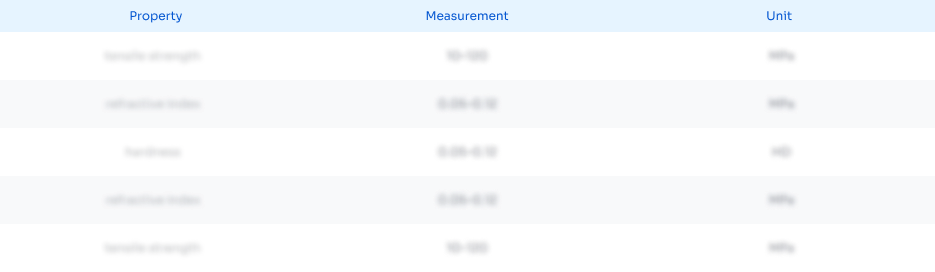
Abstract
Description
Claims
Application Information

- Generate Ideas
- Intellectual Property
- Life Sciences
- Materials
- Tech Scout
- Unparalleled Data Quality
- Higher Quality Content
- 60% Fewer Hallucinations
Browse by: Latest US Patents, China's latest patents, Technical Efficacy Thesaurus, Application Domain, Technology Topic, Popular Technical Reports.
© 2025 PatSnap. All rights reserved.Legal|Privacy policy|Modern Slavery Act Transparency Statement|Sitemap|About US| Contact US: help@patsnap.com