Adjusting method for aligning sample to axis of rotating shaft
An adjustment method and sample technology, applied in the field of sample rods, can solve the problems of easy deformation of flexible claws, inability to grasp small balls, and inability to ensure the consistency of flexible claws, etc., and achieve the effect of reducing design and manufacturing requirements
- Summary
- Abstract
- Description
- Claims
- Application Information
AI Technical Summary
Problems solved by technology
Method used
Image
Examples
Embodiment Construction
[0166] figure 1 is a multi-degree-of-freedom sample holder. like figure 2 As shown, a nanopositioner is provided on the sample rod, and the nanopositioner includes a driving part 101, a joint ball 103 and a pressing part assembly, the joint ball 103 is fixed with the driving part 101, and the pressing part assembly includes at least two pressing parts 105 and an elastic connection Component 104 , the elastic connection component 104 connects adjacent pressure pieces, the pressure piece component embraces the joint ball 103 , and there is a pre-tightening force between the pressure piece and the joint ball 103 . For example, a piezoelectric ceramic tube is used as the drive element 101 .
[0167] Pressed piece
[0168] In some embodiments, such as figure 2 As shown, each pressing piece has a concave part 1051 and a connecting part 1052 respectively, and the elastic connection assembly 104 is arranged between the connecting parts 1052 of adjacent pressing pieces, and the c...
PUM
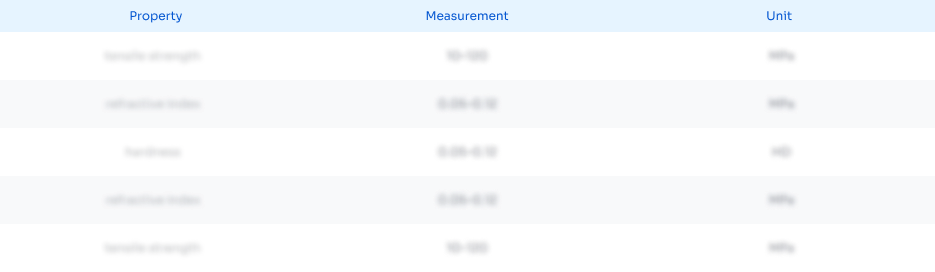
Abstract
Description
Claims
Application Information

- R&D
- Intellectual Property
- Life Sciences
- Materials
- Tech Scout
- Unparalleled Data Quality
- Higher Quality Content
- 60% Fewer Hallucinations
Browse by: Latest US Patents, China's latest patents, Technical Efficacy Thesaurus, Application Domain, Technology Topic, Popular Technical Reports.
© 2025 PatSnap. All rights reserved.Legal|Privacy policy|Modern Slavery Act Transparency Statement|Sitemap|About US| Contact US: help@patsnap.com