Coherent light-based vibration source positioning device and method
A technology of coherent light and vibration source, applied in the field of electronics, can solve the problems of missing spot images, inability to calculate the displacement of objects, inability to use, etc., to reduce environmental restrictions, improve acquisition efficiency and accuracy, and improve efficiency and accuracy. Effect
- Summary
- Abstract
- Description
- Claims
- Application Information
AI Technical Summary
Problems solved by technology
Method used
Image
Examples
Embodiment Construction
[0062] Embodiments of the present application are described below in conjunction with the accompanying drawings.
[0063] see figure 1 , figure 1 It is a schematic diagram of an application scenario of a vibration source localization device based on coherent light provided in the embodiment of the present application. Such as figure 1 As shown, the application scenario includes: a vibrating object 10 and a vibration source positioning device 20 .
[0064] Wherein, the vibrating object 10 including the vibrating source 11 can be an automatic production equipment corresponding to the field of automobile manufacturing, household appliances, transportation or food, a wearable part in a numerically controlled machine tool, or other objects such as a manipulator.
[0065] Wherein, the vibration source positioning device 20 includes: a coherent light generator 201, a lens 202, a mirror 203, a MEMS two-dimensional scanning mirror 204, a high-speed camera 205, and a processing devic...
PUM
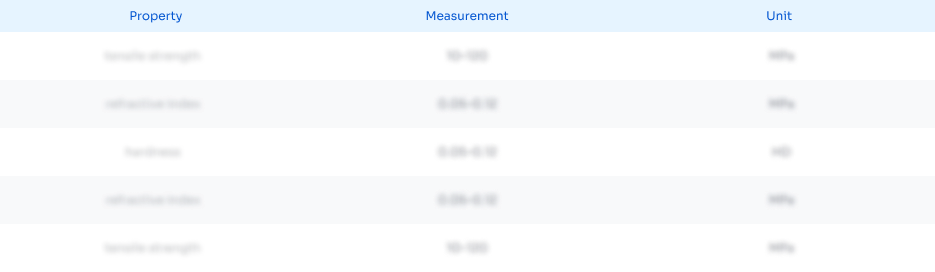
Abstract
Description
Claims
Application Information

- Generate Ideas
- Intellectual Property
- Life Sciences
- Materials
- Tech Scout
- Unparalleled Data Quality
- Higher Quality Content
- 60% Fewer Hallucinations
Browse by: Latest US Patents, China's latest patents, Technical Efficacy Thesaurus, Application Domain, Technology Topic, Popular Technical Reports.
© 2025 PatSnap. All rights reserved.Legal|Privacy policy|Modern Slavery Act Transparency Statement|Sitemap|About US| Contact US: help@patsnap.com