Plastic film production process
A technology of plastic film and production process, which is applied in the field of plastic film production and production, can solve the problems of difficult to form effective cutting, decrease of film bubble flatness, film bubble pulling and tearing, etc. Tightness, the effect of accelerating separation
- Summary
- Abstract
- Description
- Claims
- Application Information
AI Technical Summary
Problems solved by technology
Method used
Image
Examples
Embodiment Construction
[0041] In order to make the technical means, creative features, goals and effects achieved by the present invention easy to understand, the present invention will be further described below in conjunction with specific illustrations. It should be noted that, in the case of no conflict, the embodiments in the present application and the features in the embodiments can be combined with each other.
[0042] Such as Figure 1 to Figure 10 As shown, a plastic film production process uses a uniform pressing device, which includes a base plate 1, a mounting frame 2, two stretching devices 3, two pressing devices 4, a driving motor 5, and a cooling roller 6 and cutting device 7, it is characterized in that: the technique that adopts above-mentioned uniform pressing equipment to carry out plastic film production is as follows:
[0043] S1. Conveying: The free end of the blown film bubble passes through the two stretching devices 3, the two pressing devices 4, the cooling roller 6, and...
PUM
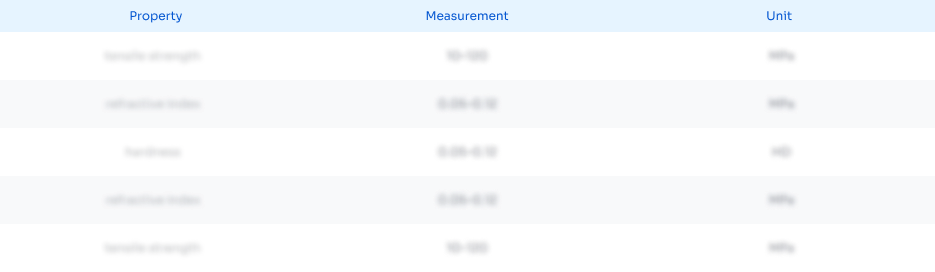
Abstract
Description
Claims
Application Information

- R&D Engineer
- R&D Manager
- IP Professional
- Industry Leading Data Capabilities
- Powerful AI technology
- Patent DNA Extraction
Browse by: Latest US Patents, China's latest patents, Technical Efficacy Thesaurus, Application Domain, Technology Topic, Popular Technical Reports.
© 2024 PatSnap. All rights reserved.Legal|Privacy policy|Modern Slavery Act Transparency Statement|Sitemap|About US| Contact US: help@patsnap.com