Method for correcting perpendicularity between Y axis sliding saddle and X axis workbench of large numerical control gantry machining center
A machining center and calibration method technology, which is applied in metal processing equipment, metal processing machine parts, manufacturing tools, etc., can solve the problems of low calibration accuracy of XY axis verticality, achieve convenient secondary calibration, reduce influence, and improve precision Effect
- Summary
- Abstract
- Description
- Claims
- Application Information
AI Technical Summary
Problems solved by technology
Method used
Image
Examples
Embodiment Construction
[0031] Step 1: The gantry base (1) is installed on the foundation, adjust the levelness of the gantry base (1), the left column (2) and the right column (3) are respectively installed in the middle of both sides of the gantry base (1), and the Y-axis beam (12) A machine tool that is installed above the left column (2) and the right column (3) at the same time to form an integral structure;
[0032] Step 2: The X-axis guide rail (6) is installed on the surface of the gantry base (1), and the X-axis workbench (5) is installed above the X-axis guide rail (6). ) to move left and right, adjust the parallelism of the X-axis guide rail (6), and correct the straightness of the X-axis travel to ensure that it is less than 0.04mm. The Y-axis beam (12) is equipped with a Y-axis guide rail (13) on the side surface. 13) The Y-axis saddle (4) is installed on it, and the Y-axis saddle (4) can move back and forth on the Y-axis guide rail (13), adjust the parallelism of the Y-axis guide rail (...
PUM
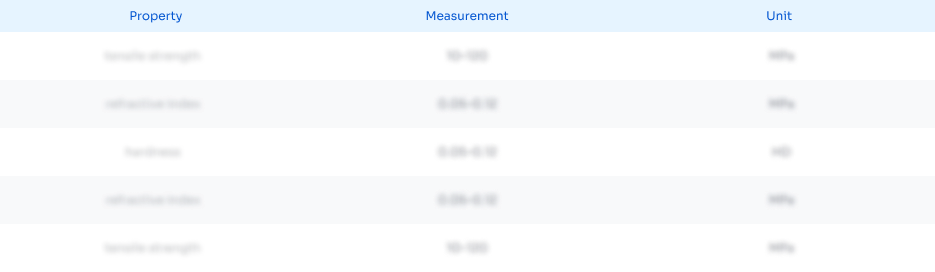
Abstract
Description
Claims
Application Information

- Generate Ideas
- Intellectual Property
- Life Sciences
- Materials
- Tech Scout
- Unparalleled Data Quality
- Higher Quality Content
- 60% Fewer Hallucinations
Browse by: Latest US Patents, China's latest patents, Technical Efficacy Thesaurus, Application Domain, Technology Topic, Popular Technical Reports.
© 2025 PatSnap. All rights reserved.Legal|Privacy policy|Modern Slavery Act Transparency Statement|Sitemap|About US| Contact US: help@patsnap.com