The welding device and process of the front window frame of the driver's cab and the welding process of the frame of the driver's cab
A welding process and welding device technology, applied in the field of rail vehicle body manufacturing, can solve the problems of many joints, affecting quality and production efficiency, and large welding heat input, so as to solve serious welding deformation, improve welding efficiency, and improve The effect of work efficiency
- Summary
- Abstract
- Description
- Claims
- Application Information
AI Technical Summary
Problems solved by technology
Method used
Image
Examples
Embodiment Construction
[0042] The present invention will be described in further detail below in conjunction with the accompanying drawings and specific embodiments:
[0043] like figure 1 and figure 2 As shown, the front window frame 1 of the driver's cab provided in this embodiment is welded on the driver's cab frame 2 , and the front window glass of the driver's cab is installed on the front window frame 1 . The front window frame 1 is an irregular structure with a three-dimensional curved surface, and is formed by splicing and welding seven profiles 3, and the section of the profiles 3 is a nearly Z-shaped structure.
[0044] like image 3 As shown, a cab front window frame welding device provided in this embodiment includes a welding platform 4 and a lifting and turning device 5. The front window frame 1 is hoisted and placed on the welding platform 4 before welding, and is completed on the welding platform 4. All splicing and welding operations. The welding platform 4 is installed on the ...
PUM
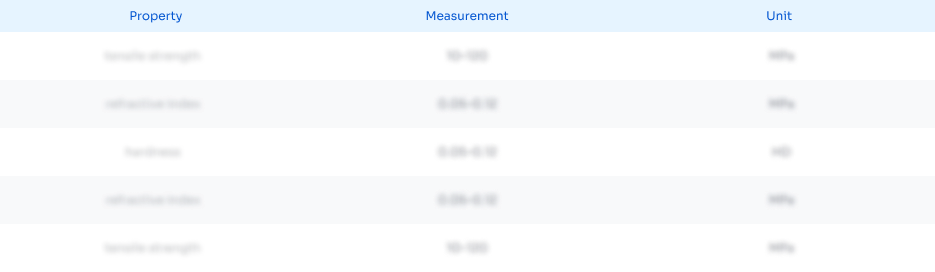
Abstract
Description
Claims
Application Information

- Generate Ideas
- Intellectual Property
- Life Sciences
- Materials
- Tech Scout
- Unparalleled Data Quality
- Higher Quality Content
- 60% Fewer Hallucinations
Browse by: Latest US Patents, China's latest patents, Technical Efficacy Thesaurus, Application Domain, Technology Topic, Popular Technical Reports.
© 2025 PatSnap. All rights reserved.Legal|Privacy policy|Modern Slavery Act Transparency Statement|Sitemap|About US| Contact US: help@patsnap.com