Method for pre-de-siliconization of vanadium slag by soda-lime roasting
A technology of soda lime and pre-desilication, applied in the field of vanadium chemical metallurgy, to achieve the effect of reducing cost, reducing vanadium loss and shortening the process flow
- Summary
- Abstract
- Description
- Claims
- Application Information
AI Technical Summary
Problems solved by technology
Method used
Image
Examples
Embodiment 1
[0039] With vanadium slag fine powder 100g, add Na 2 CO 3 20g, CaCO 3 1g, mixed and ground to obtain raw meal; then placed in a muffle furnace for roasting, the sintering temperature was 800°C, and the sintering time was 180min to obtain clinker; after the clinker was broken, it was soaked in water, and the ratio of immersion liquid to solid was 2:1 (mL / g), the leaching temperature is 60°C, the leaching time is 30min, and the qualified vanadium liquid is obtained by filtration. The V content in tailings is 0.92%, c(P)<0.01g / L, c(Si)=0.103g / L in qualified vanadium liquid. From vanadium slag to qualified vanadium liquid, the vanadium yield is 92.17%.
Embodiment 2
[0041] With vanadium slag fine powder 200g, add Na 2 CO 3 50g, CaCO 3 6g, mixed and ground to obtain raw meal; then placed in a muffle furnace for roasting, the sintering temperature was 1000°C, and the sintering time was 120min to obtain clinker; after the clinker was broken, it was soaked in water, and the ratio of immersion liquid to solid was 3:1 (mL / g), the leaching temperature is 90°C, the leaching time is 10min, and the qualified vanadium liquid is obtained by filtration. The V content in tailings is 0.95%, c(P)<0.01g / L and c(Si)=0.125g / L in qualified vanadium liquid. From vanadium slag to qualified vanadium liquid, the vanadium yield is 91.85%.
Embodiment 3
[0043] Take 500g of vanadium slag fine powder, add Na 2 CO 3 150g, CaCO 325g, mixed and ground to obtain raw meal; then placed in a muffle furnace for roasting, the sintering temperature was 1200°C, and the sintering time was 60min to obtain clinker; after the clinker was broken, it was soaked in water, and the ratio of immersion liquid to solid was 4:1 (mL / g), the leaching temperature is 30°C, the leaching time is 60min, and the qualified vanadium liquid is obtained by filtration. The V content in tailings is 0.96%, c(P)<0.01g / L, c(Si)=0.118g / L in qualified vanadium liquid. From vanadium slag to qualified vanadium liquid, the vanadium yield is 91.23%.
PUM
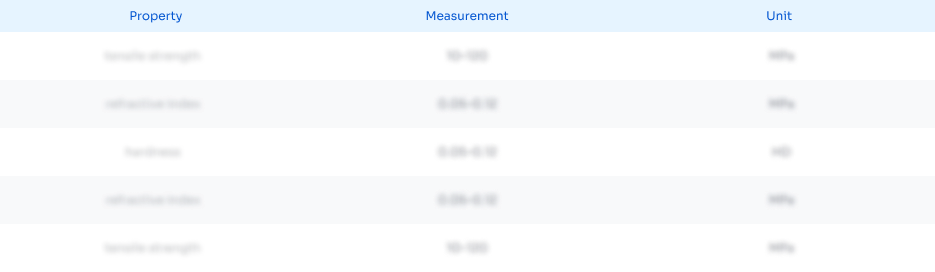
Abstract
Description
Claims
Application Information

- R&D Engineer
- R&D Manager
- IP Professional
- Industry Leading Data Capabilities
- Powerful AI technology
- Patent DNA Extraction
Browse by: Latest US Patents, China's latest patents, Technical Efficacy Thesaurus, Application Domain, Technology Topic, Popular Technical Reports.
© 2024 PatSnap. All rights reserved.Legal|Privacy policy|Modern Slavery Act Transparency Statement|Sitemap|About US| Contact US: help@patsnap.com