A kind of heat treatment method of medium carbon low alloy steel
A heat treatment method and low-alloy steel technology, applied in the field of casting casting production, can solve the problems of elongation and area shrinkage that cannot meet the standard requirements, low plasticity and mechanical properties, and easy fracture of crawler links, etc., to achieve elongation and High area shrinkage, good core plasticity and long service life
- Summary
- Abstract
- Description
- Claims
- Application Information
AI Technical Summary
Problems solved by technology
Method used
Image
Examples
Embodiment 1
[0028] A heat treatment method for medium-carbon low-alloy steel, comprising the steps of:
[0029] S1, preparation of castings: with 1E4904 type medium carbon low alloy steel material raw material, utilize mold casting to make double Kiel test block, the size mark of test block is carried out according to ASTM A703 (such as figure 1 shown).
[0030] In terms of element mass percentage, the chemical composition (%) of the above-mentioned digeer test block is: C: 0.16~0.28; Si: 0.30~0.70; Mn: 0.70~1.35; P≤0.025; S≤0.020; Cr: 0.70~ 1.10; Ni: 1.10-2.20; Mo: 0.40-0.55. The chemical composition needs to be strictly controlled, and P and S are controlled according to the lower limit.
[0031] The mechanical property control of the above-mentioned 1E4904 medium-carbon low-alloy steel is shown in Table 1:
[0032] Table 1: Mechanical property requirements of 1E4904 medium carbon low alloy steel
[0033] Rp 0.2 MPa
RPmMpa A(%) Z(%) Akv / -40℃ ≥965 ≥1138 ≥4 ...
Embodiment 2
[0040] Embodiment 2 (control group):
[0041] Using the prior art normalizing + quenching + tempering process, the same casting product was prepared as a control group. Concrete process step is identical with embodiment 1, and the casting double Kiel test block of test and the double Kiel test block of embodiment 1 are the product of pouring in the same furnace. The difference is that the "S3 annealing" step is missing, and the finished casting is obtained.
[0042] The heat treatment furnaces in Embodiment 1 and Embodiment 2 are laboratory box-type muffle furnaces.
[0043] Embodiment 1, embodiment 2 all implement 3 times, be respectively embodiment 3-6, and detect product performance, the product performance obtained, see table 2:
[0044] Table 2: Properties of 1E4904 medium carbon low alloy steel products obtained by different heat treatment processes
[0045] craft Rp 0.2 MPa
[0046] Wherein, embodiments 1, 3, and 5 are experimental groups using the proc...
PUM
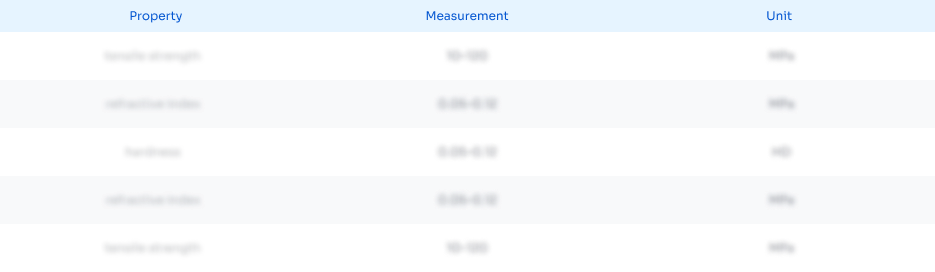
Abstract
Description
Claims
Application Information

- Generate Ideas
- Intellectual Property
- Life Sciences
- Materials
- Tech Scout
- Unparalleled Data Quality
- Higher Quality Content
- 60% Fewer Hallucinations
Browse by: Latest US Patents, China's latest patents, Technical Efficacy Thesaurus, Application Domain, Technology Topic, Popular Technical Reports.
© 2025 PatSnap. All rights reserved.Legal|Privacy policy|Modern Slavery Act Transparency Statement|Sitemap|About US| Contact US: help@patsnap.com