Method for deeply removing fluorine from LiCl solution recovered from waste batteries
A technology for used batteries and solutions, applied in battery recycling, waste collector recycling, recycling technology, etc., can solve the problems of unfavorable production, large investment, and high cost of defluorination, and achieves simple process, low production cost, and the solution to the problem. The effect of corrosion on equipment
- Summary
- Abstract
- Description
- Claims
- Application Information
AI Technical Summary
Problems solved by technology
Method used
Image
Examples
Embodiment 1
[0024] A. Raw material preparation: Take 10L of LiCl solution obtained from the recycling of waste batteries, and its fluoride ion content is measured to be 98ppm, and the mass of defluoridation agent required for calculation based on 20 times of the F content in LiCl solution is 19.6g.
[0025] B. Activation of defluorinating agent: Add 78.4ml of 2mol / L hydrochloric acid solution into the defluorinating agent according to the solid-to-liquid ratio of 1:4, mix and stir evenly to make defluorinating agent slurry.
[0026] C. Adjust the pH of the system: add the defluoridation agent slurry to the LiCl solution, and add dilute hydrochloric acid to adjust the pH of the system to 5.
[0027] D. Defluorination of LiCl solution: Mix and stir for 1 hour, and suction filter to obtain fluorine-containing residue and LiCl solution after defluorination. The fluoride ion content is 3.5ppm.
[0028] E. Defluorination agent regeneration: add fluorine-containing slag to 35g / L sodium hydroxide...
Embodiment 2
[0031] A. Raw material preparation: Take 10L of LiCl solution obtained from the recycling of waste batteries, and its fluoride ion content is measured to be 67ppm. According to 15 times the F content in the LiCl solution, the mass of defluorination agent required is 10g.
[0032] B. Activation of defluorinating agent: Add 40ml of 2mol / L hydrochloric acid solution into the defluorinating agent according to the solid-to-liquid ratio of 1:4, mix and stir evenly to make defluorinating agent slurry.
[0033] C. Adjust the pH of the system: add the defluoridation agent slurry to the LiCl solution, and add sodium carbonate to adjust the pH of the system to 5.
[0034] D. Defluorination of LiCl solution: Mix and stir for 1 hour, and filter with suction to obtain fluoride-containing residue and LiCl solution after defluorination. The fluoride ion content is 3.8ppm.
[0035] E. Regeneration of defluoridation agent: Add fluorine-containing slag to 40g / L sodium hydroxide solution at a sol...
Embodiment 3
[0038] A. Raw material preparation: take 5L of LiCl solution obtained from the recycling of waste batteries, and measure its fluoride ion content to be 84ppm. According to 15 times the F content in the LiCl solution, the mass of defluoridation agent required is 6.3g.
[0039] B. Activation of defluorinating agent: Add 78.4ml of 2mol / L hydrochloric acid solution into the defluorinating agent according to the solid-to-liquid ratio of 1:5, mix and stir evenly to prepare the defluorinating agent slurry.
[0040] C. Adjust the pH of the system: add the defluoridation agent slurry to the LiCl solution, and add dilute hydrochloric acid to adjust the pH of the system to 5.
[0041] D. Defluorination of LiCl solution: Mix and stir for 1 hour, filter with suction to obtain fluorine-containing residue and LiCl solution after defluorination, and measure the fluoride ion content to be 2.1ppm.
[0042] E. Defluorination agent regeneration: Add fluorine-containing slag to 45g / L sodium hydrox...
PUM
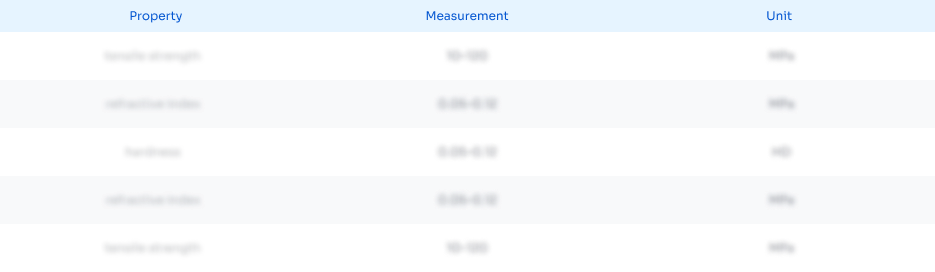
Abstract
Description
Claims
Application Information

- Generate Ideas
- Intellectual Property
- Life Sciences
- Materials
- Tech Scout
- Unparalleled Data Quality
- Higher Quality Content
- 60% Fewer Hallucinations
Browse by: Latest US Patents, China's latest patents, Technical Efficacy Thesaurus, Application Domain, Technology Topic, Popular Technical Reports.
© 2025 PatSnap. All rights reserved.Legal|Privacy policy|Modern Slavery Act Transparency Statement|Sitemap|About US| Contact US: help@patsnap.com