Sintered ore FeO content detection method and sintered ore FeO content detection system
A detection method and technology for sintered ore, which are applied in the field of FeO content detection method and system in sintered ore, and can solve the problem that the FeO content of sintered ore cannot be accurately detected in real time and the like.
- Summary
- Abstract
- Description
- Claims
- Application Information
AI Technical Summary
Problems solved by technology
Method used
Image
Examples
Embodiment 1
[0079] refer to figure 1 , the method for detecting FeO content in sintered ore provided by Embodiment 1 of the present invention includes:
[0080] Step S101, acquiring a thermal image, and extracting a key frame image in combination with the change law of the dust at the tail of the sintering machine;
[0081] Step S102, according to the key frame image, using the geometric characteristics of the tail trolley, extracting the infrared thermal image of interest, so as to obtain the infrared thermal image of the sintered ore section;
[0082] Step S103, based on the infrared thermal image of the cross-section of the sinter, extracting shallow-level features and deep-level features describing the quality of the sinter;
[0083] Step S104, establishing a multiphase thermodynamic model of the sintering process based on the Gibbs free energy theorem, and according to the multiphase thermodynamic model, obtain the FeO content classification characteristics at the highest temperatur...
Embodiment 2
[0089] refer to figure 2 , the method for detecting FeO content in sintered ore provided by Embodiment 2 of the present invention includes:
[0090] In step S201, a thermal image is obtained, and a key frame image is extracted in combination with the change law of the dust at the tail of the sintering machine.
[0091] Specifically, this embodiment also includes setting up an online FeO content detection system based on infrared thermal imager imaging before obtaining thermal images, see for details image 3 , including a distribution machine 10, an igniter 20, a sintering machine tail 30, a temperature measuring device 40, an optical fiber 50, a universal platform 60 and a computer 70. The uncooled focal plane infrared thermal imaging camera is installed at the universal platform of the observation window at the tail of the sintering machine to collect real-time temperature information of the blanking material at the tail of the machine. The temperature information is trans...
Embodiment 3
[0278] In this embodiment, the 360m 2 The sintering machine is used as an experimental platform, and the invented measuring device is applied to the detection of FeO content in the section of the sintered material at the end of the machine. On-site measurement systems such as image 3 As shown, the detection device is installed at the universal platform of the observation window at the tail of the sintering machine, and the temperature information is transmitted by optical fiber to the computer in the central control room for data processing. Figure 8 As shown, the details are as follows:
[0279] Firstly, fix the end of the sintering machine with a universal pan-tilt, set up an infrared thermal imager to take pictures of the cutting area of the sintering machine in the observation window; then obtain the blanking cycle according to the speed of the on-site sintering machine, and extract the key points from the image smoke detection value in one cycle Frame the image, ext...
PUM
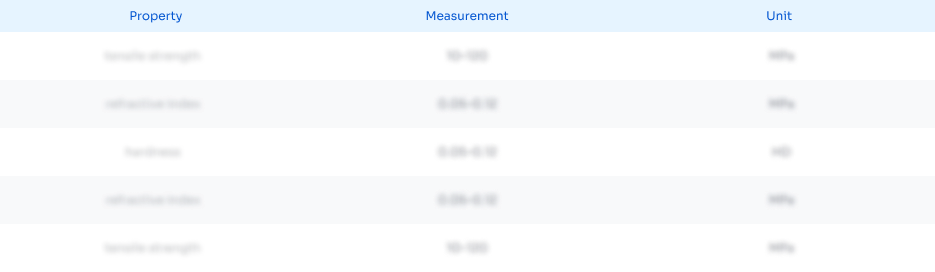
Abstract
Description
Claims
Application Information

- Generate Ideas
- Intellectual Property
- Life Sciences
- Materials
- Tech Scout
- Unparalleled Data Quality
- Higher Quality Content
- 60% Fewer Hallucinations
Browse by: Latest US Patents, China's latest patents, Technical Efficacy Thesaurus, Application Domain, Technology Topic, Popular Technical Reports.
© 2025 PatSnap. All rights reserved.Legal|Privacy policy|Modern Slavery Act Transparency Statement|Sitemap|About US| Contact US: help@patsnap.com