Post-finishing process for superfine fiber pile fabrics
A microfiber and post-finishing technology, which is applied in fiber treatment, textile material treatment, continuous treatment of textile materials, etc., can solve the problems affecting the wearing comfort of clothing fabrics, reduce the amount of waste water produced, ensure uniform adhesion, Promotes even dispersion
- Summary
- Abstract
- Description
- Claims
- Application Information
AI Technical Summary
Problems solved by technology
Method used
Examples
Embodiment 1
[0036] (1) Pretreatment of microfiber pile sports fabric: 5kg superfine fiber pile sports fabric is humidified until the water content reaches 70wt%, and then transferred to -10 ℃ cold storage environment to stand for 1h, and used immediately after taking it out from the cold storage The hot pressing machine carries out the hot pressing treatment for 10 minutes, the hot pressing pressure is 8 MPa, the hot pressing temperature is 120 ° C, and then dried at 70 ° C, that is, the pretreatment is completed;
[0037] (2) Preparation of finishing solution: heat 90kg of water to 65°C, add 5kg of zinc oxide and 5kg of polyoxyethylene lauryl ether sodium sulfate, stir and disperse evenly, and obtain a finishing solution;
[0038] (3) After-finishing: immerse the superfine fiber pile sports fabric after the above-mentioned pretreatment in the finishing solution, control the bath ratio at 1:15, and roll off the excess finishing solution after immersion for 30 minutes, the rolling rate is 7...
Embodiment 2
[0041] The hot-pressing treatment time among the embodiment 1 is replaced by 5min, all the other are exactly the same as embodiment 1.
[0042] (1) Pretreatment of microfiber pile sports fabric: 5kg superfine fiber pile sports fabric is humidified until the water content reaches 70wt%, and then transferred to -10 ℃ cold storage environment to stand for 1h, and used immediately after taking it out from the cold storage The hot pressing machine carries out the hot pressing treatment for 5 minutes, the hot pressing pressure is 8 MPa, the hot pressing temperature is 120 ° C, and then dried at 70 ° C, that is, the pretreatment is completed;
[0043] (2) Preparation of finishing solution: heat 90kg of water to 65°C, add 5kg of zinc oxide and 5kg of polyoxyethylene lauryl ether sodium sulfate, stir and disperse evenly, and obtain a finishing solution;
[0044] (3) After-finishing: immerse the superfine fiber pile sports fabric after the above-mentioned pretreatment in the finishing s...
Embodiment 3
[0058] The antistatic agent in embodiment 1 is replaced by zinc methacrylate by zinc oxide, and all the other are exactly the same as embodiment 1.
[0059] (1) Pretreatment of microfiber pile sports fabric: 5kg superfine fiber pile sports fabric is humidified until the water content reaches 70wt%, and then transferred to -10 ℃ cold storage environment to stand for 1h, and used immediately after taking it out from the cold storage The hot pressing machine carries out the hot pressing treatment for 10 minutes, the hot pressing pressure is 8 MPa, the hot pressing temperature is 120 ° C, and then dried at 70 ° C, that is, the pretreatment is completed;
[0060] (2) Preparation of finishing solution: heat 90kg of water to 65°C, add 5kg of zinc methacrylate and 5kg of polyoxyethylene lauryl ether sodium sulfate, stir and disperse evenly, and obtain a finishing solution;
[0061] (3) After-finishing: immerse the superfine fiber pile sports fabric after the above-mentioned pretreatme...
PUM
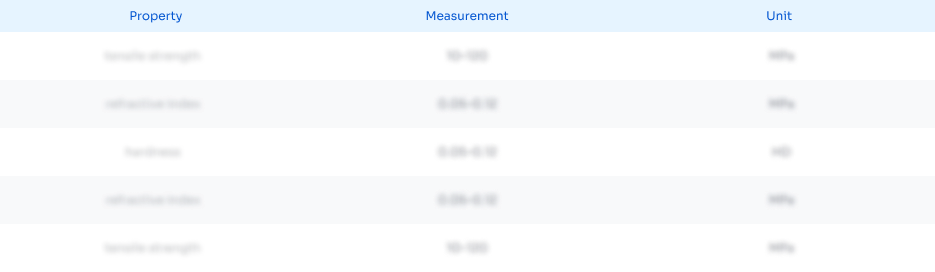
Abstract
Description
Claims
Application Information

- R&D Engineer
- R&D Manager
- IP Professional
- Industry Leading Data Capabilities
- Powerful AI technology
- Patent DNA Extraction
Browse by: Latest US Patents, China's latest patents, Technical Efficacy Thesaurus, Application Domain, Technology Topic, Popular Technical Reports.
© 2024 PatSnap. All rights reserved.Legal|Privacy policy|Modern Slavery Act Transparency Statement|Sitemap|About US| Contact US: help@patsnap.com