Multi-time mode-locking hydraulic oil path structure of injection molding machine and multi-time mode-locking method thereof
A hydraulic oil circuit and injection molding machine technology, which is applied in the field of hydraulic oil circuit structure, can solve problems such as warping, exhaust effect, and deformation of injection molds, etc., to prolong the life of spare parts, eliminate pressure shock, and improve mechanical properties. Effect
- Summary
- Abstract
- Description
- Claims
- Application Information
AI Technical Summary
Problems solved by technology
Method used
Image
Examples
Embodiment Construction
[0034] Below, the present invention will be further described in conjunction with the accompanying drawings and specific implementation methods. It should be noted that, under the premise of not conflicting, the various embodiments described below or the technical features can be combined arbitrarily to form new embodiments. .
[0035] The multiple clamping hydraulic oil circuit structure of the injection molding machine of the present invention is as follows: Figure 1-Figure 5 As shown, it includes an oil tank for storing hydraulic oil, a first oil pump 6 for delivering hydraulic oil, an oil pump for the main oil circuit, a servo motor 5 for powering the oil pump, communicating with the oil pump and used to drive the mold opening and closing Clamping high-pressure cylinder;
[0036] The first control valve 1 used to control the on-off of the first oil pump 6 and the second control valve used to control the conduction of the hydraulic oil to the mold-clamping high-pressure c...
PUM
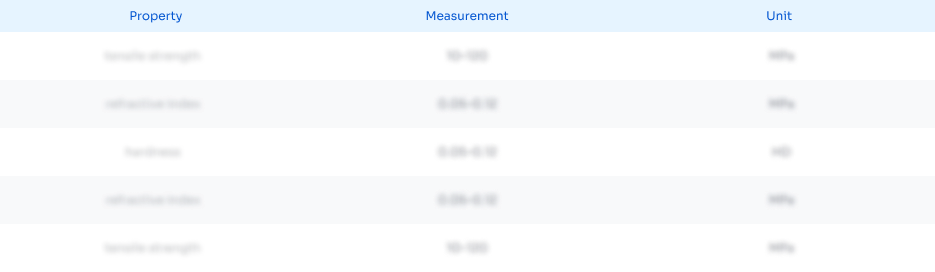
Abstract
Description
Claims
Application Information

- R&D Engineer
- R&D Manager
- IP Professional
- Industry Leading Data Capabilities
- Powerful AI technology
- Patent DNA Extraction
Browse by: Latest US Patents, China's latest patents, Technical Efficacy Thesaurus, Application Domain, Technology Topic, Popular Technical Reports.
© 2024 PatSnap. All rights reserved.Legal|Privacy policy|Modern Slavery Act Transparency Statement|Sitemap|About US| Contact US: help@patsnap.com