Vertical machining tool
A processing machine tool and vertical technology, which is applied in the direction of metal processing machinery parts, metal processing equipment, manufacturing tools, etc., can solve the problems of spindle rotation and other problems, and achieve the effect of ensuring processing accuracy
- Summary
- Abstract
- Description
- Claims
- Application Information
AI Technical Summary
Problems solved by technology
Method used
Image
Examples
Embodiment 1
[0022] like Figure 3-5 As shown, a vertical processing machine tool includes a bed 5 and a Z-axis sliding table 1. Two columns 2 are fixedly connected to the bed. The Z-axis slide rail 3 is slidably connected, and the middle part of the Z-axis slide table 1 is provided with a main shaft 4 , and the main shaft 4 is located below the Z-axis slide table 1 . The column 2 is fixedly connected with the bed 5, the relative movement of the workpiece and the spindle 4 in the horizontal direction is realized by the relative movement of the worktable and the spindle 4, and the relative movement of the workpiece and the spindle 4 in the vertical direction is realized by the movement of the Z-axis slide table 1 Realize that when the Z-axis sliding table 1 moves, in addition to the vertical movement, there is also a horizontal movement, and the workbench needs to be moved accordingly to eliminate the influence of the Z-axis sliding table 1 movement. Since the main shaft 4 is located direc...
Embodiment 2
[0027] The difference between this embodiment and Embodiment 1 is that the angle between the Z-axis slide rail 3 and the horizontal plane is 30°, the Z-axis slide rail 3 is located on the top surface of the column 2, and the angle between the top surface of the column 2 and the horizontal plane is 30°. °. The Z-axis slide rail 3 is perpendicular to the Y-axis slide rail 8 . When the Z-axis slide table 1 moves along the Z-axis slide rail 3, the X-axis slide table 7 needs to move along the X-axis slide rail 9 to eliminate the influence.
Embodiment 3
[0029] The difference between this embodiment and Embodiment 1 is that the angle between the Z-axis slide rail 3 and the horizontal plane is 60°, the Z-axis slide rail 3 is located on the top surface of the column 2, and the angle between the top surface of the column 2 and the horizontal plane is 50°. °. At this time, there is a certain angle between the orthographic projection of the Z-axis slide rail 3 on the top surface of the bed 5 and the Y-axis slide rail 8 and the X-axis slide rail 9 . When the Z-axis slide 1 moves along the Z-axis slide 3, the X-axis slide 7 needs to move along the X-axis slide 9, and the Y-axis slide 6 moves along the Y-axis slide 8 to eliminate the movement of the Z-axis slide 1. Impact.
PUM
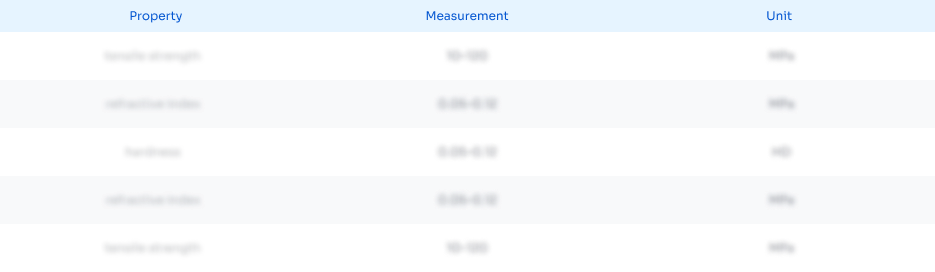
Abstract
Description
Claims
Application Information

- R&D
- Intellectual Property
- Life Sciences
- Materials
- Tech Scout
- Unparalleled Data Quality
- Higher Quality Content
- 60% Fewer Hallucinations
Browse by: Latest US Patents, China's latest patents, Technical Efficacy Thesaurus, Application Domain, Technology Topic, Popular Technical Reports.
© 2025 PatSnap. All rights reserved.Legal|Privacy policy|Modern Slavery Act Transparency Statement|Sitemap|About US| Contact US: help@patsnap.com