Engineering plastic bearing cage
A technology of engineering plastics and cages, which is applied to bearing components, shafts, shafts and bearings, etc., can solve the problems that it is difficult to adapt to high-precision bearings, thick-walled holes are prone to defects, and the accuracy of cages is difficult to guarantee. Hole defects, shorter molding cycle, no effect on strength
- Summary
- Abstract
- Description
- Claims
- Application Information
AI Technical Summary
Problems solved by technology
Method used
Image
Examples
Embodiment Construction
[0025] The present invention will be described in detail below in conjunction with the accompanying drawings and embodiments. However, it should be understood that the accompanying drawings are provided only for better understanding of the present invention, and they should not be construed as limiting the present invention.
[0026] like Figure 1~3 As shown, the present invention provides an engineering plastic cage, which includes a cage main body 1, on the cage main body 1 and along its circumference, several window holes 11 for installing rollers are arranged at intervals, and two adjacent windows A window beam 12 is formed between the holes 11; a notch 13 is provided on the outer diameter side of each window beam 12 to reduce the wall thickness of the window beam 12 of the cage main body 1, so that the wall thickness of the cage main body 1 can be reduced during the injection molding process. More uniform and stable shrinkage in the middle, improve the precision of the ...
PUM
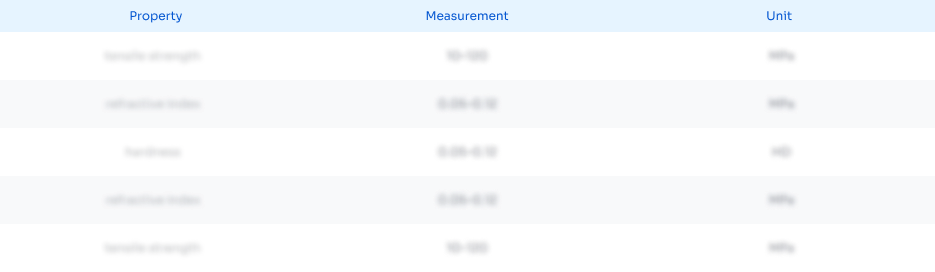
Abstract
Description
Claims
Application Information

- R&D
- Intellectual Property
- Life Sciences
- Materials
- Tech Scout
- Unparalleled Data Quality
- Higher Quality Content
- 60% Fewer Hallucinations
Browse by: Latest US Patents, China's latest patents, Technical Efficacy Thesaurus, Application Domain, Technology Topic, Popular Technical Reports.
© 2025 PatSnap. All rights reserved.Legal|Privacy policy|Modern Slavery Act Transparency Statement|Sitemap|About US| Contact US: help@patsnap.com