Resistance spot welding method and method of manufacturing welded member
A technology of resistance spot welding and welding conditions, applied in resistance welding equipment, manufacturing tools, welding power sources, etc., can solve the problem of inability to ensure the diameter of the nugget, and achieve the effect of improving the yield
- Summary
- Abstract
- Description
- Claims
- Application Information
AI Technical Summary
Problems solved by technology
Method used
Image
Examples
Embodiment
[0145] For the group of two or three overlapping metal plates shown in Table 1, carry out trial welding under the conditions shown in Table 1, and then, for the two or three overlapping metal plates shown in Table 2 The plate group of the plates is subjected to full-scale welding under the conditions shown in Table 2 to produce welded joints.
[0146] Here, trial welding and formal welding are figure 1 and figure 2 the interference-free state shown, and Figure 3-6 The state of simulated disturbance is shown. In the drawings, reference numerals 11, 12, and 13 are metal plates, 14 is an electrode, 15 is a spacer, and 16 is a welded point. It should be noted that, if image 3 and Figure 4 As shown, two welded points 16 are provided, and the welding position (the center between the electrodes) is adjusted so that the welded points are in the middle (same as the distance L between the welded points). In addition, in Figure 5 and Figure 6 Among them, spacers 15 are inse...
PUM
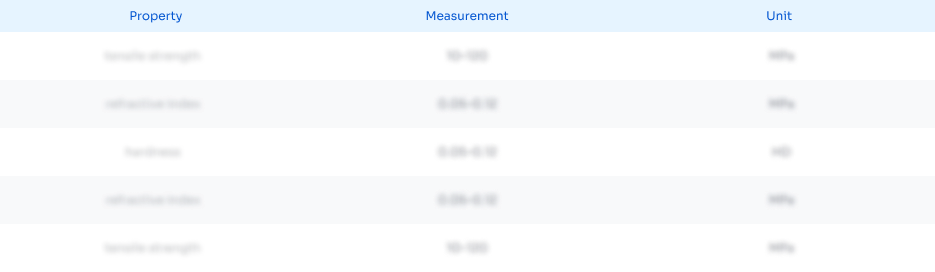
Abstract
Description
Claims
Application Information

- R&D Engineer
- R&D Manager
- IP Professional
- Industry Leading Data Capabilities
- Powerful AI technology
- Patent DNA Extraction
Browse by: Latest US Patents, China's latest patents, Technical Efficacy Thesaurus, Application Domain, Technology Topic, Popular Technical Reports.
© 2024 PatSnap. All rights reserved.Legal|Privacy policy|Modern Slavery Act Transparency Statement|Sitemap|About US| Contact US: help@patsnap.com