A motor function safety control method and device
A functional safety and control method technology, applied in the direction of motor control, control system, electrical components, etc., can solve the problem of inability to accurately control the overload operation of the motor, and achieve the effect of improving overload performance and increasing torque density
- Summary
- Abstract
- Description
- Claims
- Application Information
AI Technical Summary
Problems solved by technology
Method used
Image
Examples
Embodiment 2
[0165] Corresponding to the motor function safety control method described in the above embodiments, Image 6 A structural block diagram of the motor functional safety control device provided by the embodiment of the present application is shown, and for the convenience of description, only the parts related to the embodiment of the present application are shown.
[0166] refer to Image 6 , the device 200 includes:
[0167] The first obtaining module 101 is used to obtain the control command data sent by the host computer;
[0168] The second acquiring module 102 is used to acquire the running data of the motor;
[0169] A calculation module 103, configured to calculate the operation data and obtain safe operation data of the motor;
[0170] A comparison module 104, configured to compare the size of the control command data and the safe operation data;
[0171] The first judging module 105 is configured to send the control command data to the motor controller if the contr...
Embodiment 3
[0181] Figure 8 A schematic structural diagram of the motor functional safety controller provided in this embodiment. like Figure 8 As shown, the motor functional safety controller 30 of this embodiment includes: at least one processor 300 ( Figure 8 only shows one) processor, memory 301, and a computer program or embedded system program 302 stored in said memory 301 and operable on said at least one processor 300, said processor 300 executing said computer Program 302 is to implement the steps in any of the embodiments of the motor function safety control method described above.
[0182] The motor functional safety controller 30 can be a computing device such as an embedded system, an industrial computer, a desktop computer, a notebook, a palmtop computer, and a cloud server. The motor functional safety controller may include, but not limited to, a processor 300 and a memory 301 . Those skilled in the art can understand that, Figure 8 It is only an example of the mot...
PUM
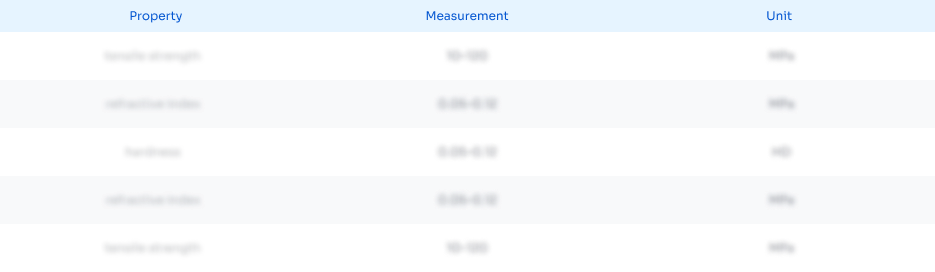
Abstract
Description
Claims
Application Information

- R&D
- Intellectual Property
- Life Sciences
- Materials
- Tech Scout
- Unparalleled Data Quality
- Higher Quality Content
- 60% Fewer Hallucinations
Browse by: Latest US Patents, China's latest patents, Technical Efficacy Thesaurus, Application Domain, Technology Topic, Popular Technical Reports.
© 2025 PatSnap. All rights reserved.Legal|Privacy policy|Modern Slavery Act Transparency Statement|Sitemap|About US| Contact US: help@patsnap.com