Method and device for improving micro-deformation loading accuracy
A loading device and micro-deformation technology, which is applied in the direction of measuring device, using repeated force/pulsation force to test the strength and strength characteristics of materials, etc., can solve the problem of reducing the uncertainty of micro-deformation loading device and large uncertainty of micro-deformation loading, etc. problem, to achieve the effect of uniform deformation loading in the whole field, high accuracy of repeated loading, and elimination of thread gap
- Summary
- Abstract
- Description
- Claims
- Application Information
AI Technical Summary
Problems solved by technology
Method used
Image
Examples
Embodiment Construction
[0024] Such as figure 1 As shown, this embodiment relates to a device for improving the accuracy of micro-deformation loading, including: a test piece assembly composed of a fastening screw test piece 1, a thin-walled disc part test piece 2, a fastening screw sleeve test piece 3, and a coupling And the piezoelectric actuator 10, wherein: the test piece assembly and the driving end of the piezoelectric actuator 10 are connected by a rigid coupling, the test piece assembly is fixedly arranged on the base, and the piezoelectric actuator 10 is fixedly arranged on the actuator On the base 11 of the test piece, when the piezoelectric actuator 10 produces a specified displacement and drives the rigid coupling to drive the central area of the test piece assembly to produce a same displacement.
[0025] Between the fastening screw test piece 1 and the thin-walled disc part test piece 2 and between the thin-walled disc part test piece 2 and the fastening screw sleeve test piece 3, all...
PUM
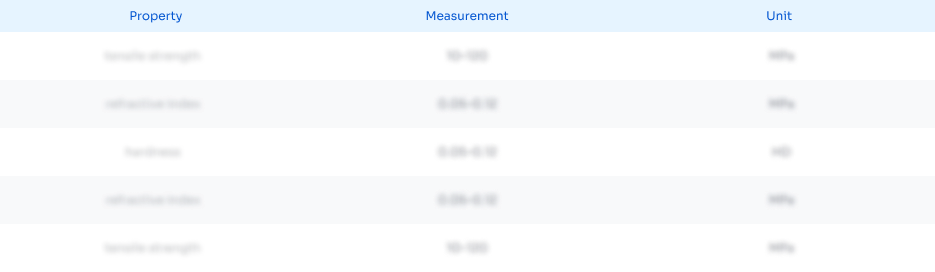
Abstract
Description
Claims
Application Information

- Generate Ideas
- Intellectual Property
- Life Sciences
- Materials
- Tech Scout
- Unparalleled Data Quality
- Higher Quality Content
- 60% Fewer Hallucinations
Browse by: Latest US Patents, China's latest patents, Technical Efficacy Thesaurus, Application Domain, Technology Topic, Popular Technical Reports.
© 2025 PatSnap. All rights reserved.Legal|Privacy policy|Modern Slavery Act Transparency Statement|Sitemap|About US| Contact US: help@patsnap.com