Manipulator structure and robot capable of achieving switching between adsorption and clamping modes
A manipulator, dual-mode technology, applied in the field of stacking robots, can solve problems such as the inability to achieve multiple modes of work and switching, and a single working mode.
- Summary
- Abstract
- Description
- Claims
- Application Information
AI Technical Summary
Problems solved by technology
Method used
Image
Examples
Embodiment 1
[0049] A manipulator structure capable of switching between two modes of adsorption and gripping, including a screw box 1 and an execution unit;
[0050] The screw box 1 includes a box body, No. 1 servo motor 101, screw mandrel 102, moving nut 103, No. 1 hydraulic cylinder 105 and chuck 106; No. 1 servo motor 101 is installed on the left side wall inside the box body, and No. 1 servo motor The output end of 101 protrudes horizontally to the right and is connected with a screw rod 102, the right end of the screw rod 102 is rotationally connected with the right side wall of the box; the moving nut 103 is screwed on the screw rod 102, and a No. 1 hydraulic cylinder 105 is installed at the bottom of the moving nut 103 , the telescopic end of the No. 1 hydraulic cylinder 105 protrudes downwards from the box and is connected with a chuck 106; the bottom of the box corresponds to the moving path of the moving nut 103 and has a corresponding type of slideway 101;
[0051] The executio...
Embodiment 2
[0054] A manipulator structure capable of switching between two modes of adsorption and gripping, including a screw box 1 and an execution unit;
[0055] The screw box 1 includes a box body, No. 1 servo motor 101, screw mandrel 102, moving nut 103, No. 1 hydraulic cylinder 105 and chuck 106; No. 1 servo motor 101 is installed on the left side wall inside the box body, and No. 1 servo motor The output end of 101 protrudes horizontally to the right and is connected with a screw rod 102, the right end of the screw rod 102 is rotationally connected with the right side wall of the box; the moving nut 103 is screwed on the screw rod 102, and a No. 1 hydraulic cylinder 105 is installed at the bottom of the moving nut 103 , the telescopic end of the No. 1 hydraulic cylinder 105 protrudes downwards from the box and is connected with a chuck 106; the bottom of the box corresponds to the moving path of the moving nut 103 and has a corresponding type of slideway 101;
[0056] The executio...
Embodiment 3
[0060] A manipulator structure capable of switching between two modes of adsorption and gripping, including a screw box 1 and an execution unit;
[0061] The screw box 1 includes a box body, No. 1 servo motor 101, screw mandrel 102, moving nut 103, No. 1 hydraulic cylinder 105 and chuck 106; No. 1 servo motor 101 is installed on the left side wall inside the box body, and No. 1 servo motor The output end of 101 protrudes horizontally to the right and is connected with a screw rod 102, the right end of the screw rod 102 is rotationally connected with the right side wall of the box; the moving nut 103 is screwed on the screw rod 102, and a No. 1 hydraulic cylinder 105 is installed at the bottom of the moving nut 103 , the telescopic end of the No. 1 hydraulic cylinder 105 protrudes downwards from the box and is connected with a chuck 106; the bottom of the box corresponds to the moving path of the moving nut 103 and has a corresponding type of slideway 101;
[0062] The executio...
PUM
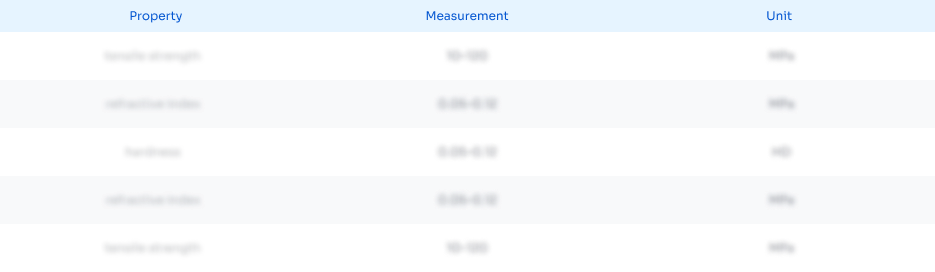
Abstract
Description
Claims
Application Information

- R&D Engineer
- R&D Manager
- IP Professional
- Industry Leading Data Capabilities
- Powerful AI technology
- Patent DNA Extraction
Browse by: Latest US Patents, China's latest patents, Technical Efficacy Thesaurus, Application Domain, Technology Topic, Popular Technical Reports.
© 2024 PatSnap. All rights reserved.Legal|Privacy policy|Modern Slavery Act Transparency Statement|Sitemap|About US| Contact US: help@patsnap.com