Battery-grade lithium hydroxide monohydrate production process applying novel combined calcium removal
A monohydrate lithium hydroxide, production process technology, applied in the direction of lithium oxide;/hydroxide, sulfate/bisulfate preparation, alkali metal sulfite/sulfate dehydration, etc., can solve the problem of calcium content, Affect the decalcification process, the effect of decalcification is poor, etc., to achieve the effect of reducing the content of calcium salt
- Summary
- Abstract
- Description
- Claims
- Application Information
AI Technical Summary
Problems solved by technology
Method used
Image
Examples
Embodiment 1
[0020] Such as figure 1 As shown, the present invention applies the battery-grade monohydrate lithium hydroxide production process of novel joint descaling, comprising the following steps: (1) spodumene is sequentially calcined, cooled, finely ground, acid reaction, and the After the product is cooled to 80°C, it is adjusted into a slurry with water, and the solid content of the slurry is 60%;
[0021] (2) Add calcium salt to the above slurry and stir for leaching. The calcium salt is mixed with water to form a slurry with a solid content of 55%. The temperature in the leaching tank is 50°C and pH=5. Afterwards, use a filter press to filter and use tap water Or the filter cake is rinsed with process water, and the filter cake is purged with compressed air so that the water content of the filter cake is 20%, and the rinse water is returned to step (1) for pulping, and the filtered clear liquid is purified with an alkaline solution. Adjust the pH value to 12, and remove the imp...
Embodiment 2
[0028] The production process of battery-grade lithium hydroxide monohydrate using a new type of joint decalcification includes the following steps:
[0029] (1) The spodumene is sequentially calcined, cooled, finely ground, and reacted with acid, and the product to be reacted with acid is cooled to 90° C. and then mixed with water to form a slurry with a solid content of 70%;
[0030] (2) Add calcium salt to the above slurry and stir for leaching, the calcium salt is adjusted to slurry with water, the solid content is 50%, the temperature in the leaching tank is 60 ° C, pH = 7, and then use a filter press to filter and use tap water Or the filter cake is rinsed with process water, and the filter cake is purged with compressed air to make the water content of the filter cake = 15%, and the rinse water is returned to step (1) for pulping, and the filtered clear liquid is purified with lithium hydroxide solution , adjust the pH value to 10, and remove the impurity iron, manganes...
PUM
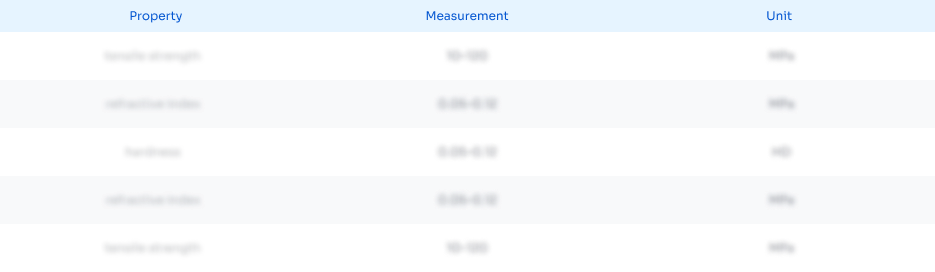
Abstract
Description
Claims
Application Information

- R&D Engineer
- R&D Manager
- IP Professional
- Industry Leading Data Capabilities
- Powerful AI technology
- Patent DNA Extraction
Browse by: Latest US Patents, China's latest patents, Technical Efficacy Thesaurus, Application Domain, Technology Topic, Popular Technical Reports.
© 2024 PatSnap. All rights reserved.Legal|Privacy policy|Modern Slavery Act Transparency Statement|Sitemap|About US| Contact US: help@patsnap.com