Casting method of flat ingot for electrolytic condenser
A technology for electrolytic capacitors and flat ingots is applied in the field of aluminum product casting, which can solve the problems of increased ingot grain coarsening tendency, formation of slag inclusions, impurity cannot be separated in time, etc., and achieves the effect of uniform structure and no defects in appearance.
- Summary
- Abstract
- Description
- Claims
- Application Information
AI Technical Summary
Problems solved by technology
Method used
Image
Examples
Embodiment 1
[0030] During the casting process, the casting temperature is controlled at 700°C-710°C, and then the casting speed and cooling water flow are adjusted. When the casting speed is controlled at 47mm / min, with the cooling water flow from 128m 3 / h began to increase, during which the water flow was 128m 3 / h, aluminum leakage occurs during startup, such as figure 1 shown. Then, the water flow is controlled at 151m 3 / h, the thermal tumor of the ingot is reduced to less than 3mm, such as figure 2 As shown in ①, it meets the standard of thermal tumor thickness ≤ 3mm. Cooling water flow at 151m 3 / h-192m 3 / h, thermal bumps and cold barriers meet the standard of ≤3mm, and the grain size meets the standard of 3-7 per square decimeter, such as figure 2 As shown in ②, when the cooling water flow is greater than 192m 3 / h, the cold barrier exceeds the requirement of ≤3mm, such as figure 2 As shown in ③.
[0031] Therefore, a set of parameter ranges is obtained: casting tempe...
Embodiment 2
[0033] During the casting process, control the casting temperature at 700°C-710°C, then adjust the casting speed and cooling water flow, when the cooling water flow is controlled at 180m 3 / h, as the casting speed increases from 38mm / min, faults appear on the surface of the slab, such as image 3 shown. Then, cold barrier defects start to appear see Figure 4 , as the speed increases, the cold gap decreases, and the change trend is shown in Figure 5 As shown in ①, when the casting speed is controlled at 41mm / min-50mm / min, the surface defects of the slab, heat bumps, and cold snaps meet the standard of ≤3mm, and the grain size meets the standard of 3-7 per square decimeter. See Figure 5 As shown in ②, when the casting speed is greater than 50mm / min, the thermal tumor will increase significantly, such as Figure 5 As shown in ③.
[0034] Therefore, a set of parameter ranges is obtained: casting temperature 700°C-710°C; casting speed 41mm / min-50mm / min; cooling water flow 1...
Embodiment 3
[0036] During the casting process, the casting speed is 47mm / min, and the cooling water flow rate is 180m 3 / h control, and then adjust the casting temperature from 679°C, some casting failures and large-area thermal tumors occur due to low temperature, see Figure 6 and Figure 7 . After the casting temperature is from 679℃, the size of the thermal nodules shows a downward trend, see Figure 8 As shown in ①. When the casting temperature is controlled at 685-730°C, the surface defects of the slab, heat bumps, and cold snaps meet the standard of ≤3mm, and the grain size meets the standard of 3-7 per square decimeter, see Figure 8 As shown in ②. When the casting temperature is higher than 730°C, the metal nodules and grains become significantly larger, see Figure 8 As shown in ③.
[0037] Therefore, a set of parameter ranges is obtained: casting temperature 685°C-730°C; casting speed 47mm / min; cooling water flow 180m 3 / h.
[0038] Select process parameters according t...
PUM
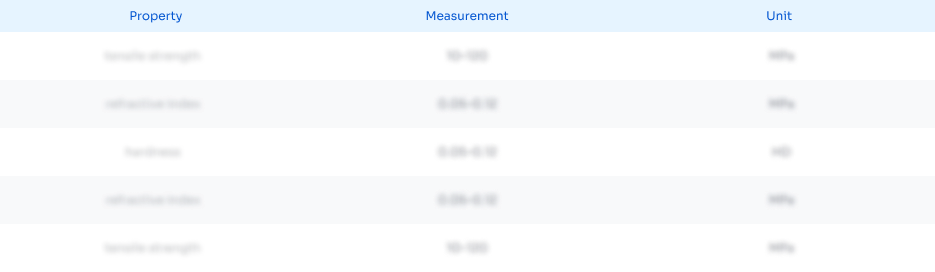
Abstract
Description
Claims
Application Information

- R&D Engineer
- R&D Manager
- IP Professional
- Industry Leading Data Capabilities
- Powerful AI technology
- Patent DNA Extraction
Browse by: Latest US Patents, China's latest patents, Technical Efficacy Thesaurus, Application Domain, Technology Topic, Popular Technical Reports.
© 2024 PatSnap. All rights reserved.Legal|Privacy policy|Modern Slavery Act Transparency Statement|Sitemap|About US| Contact US: help@patsnap.com