Turbine disk cavity sealing structure with bypass bleed air
A turbine disk and bleed air technology, applied in the direction of leakage prevention, engine components, machines/engines, etc., can solve the problems of increasing the risk of airflow separation at the root of the rotor blade, the intensity of secondary flow loss, the reduction of turbine efficiency, and the increase of flow loss in turbine passages, etc. , to achieve the effects of good economy and realizability, reduced secondary flow loss, and improved turbine efficiency
- Summary
- Abstract
- Description
- Claims
- Application Information
AI Technical Summary
Problems solved by technology
Method used
Image
Examples
Embodiment Construction
[0037] In order to make the object, technical solution and advantages of the present invention clearer, the present invention will be described in further detail below in conjunction with specific embodiments and with reference to the accompanying drawings.
[0038] The sealing structure of the turbine disc cavity with bypass bleed air proposed by the present invention is as follows: figure 2 shown.
[0039] Including an inner support ring assembly 1 and a front baffle assembly 2, the inner support ring assembly 1 is provided with a pre-rotation nozzle 3.
[0040] The inner support ring assembly 1 also includes a first honeycomb structure 101, a single grate structure 102, and a three-grate structure 103;
[0041] The front baffle assembly 2 includes a front baffle air inlet 201, two grate structures 202, a second honeycomb structure 203, and a third honeycomb structure 204;
[0042] The first honeycomb structure 101 and the two grate structures 202 form a sealing gap;
[...
PUM
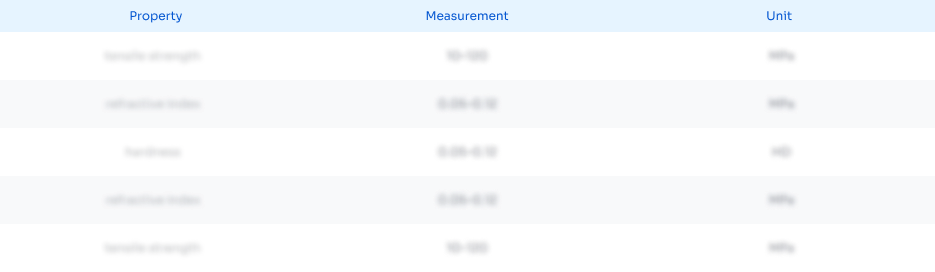
Abstract
Description
Claims
Application Information

- R&D
- Intellectual Property
- Life Sciences
- Materials
- Tech Scout
- Unparalleled Data Quality
- Higher Quality Content
- 60% Fewer Hallucinations
Browse by: Latest US Patents, China's latest patents, Technical Efficacy Thesaurus, Application Domain, Technology Topic, Popular Technical Reports.
© 2025 PatSnap. All rights reserved.Legal|Privacy policy|Modern Slavery Act Transparency Statement|Sitemap|About US| Contact US: help@patsnap.com