A multi-constraint machining optimization method for coordinated manipulators based on velocity reconfiguration
An optimization method and technology of robotic arms, applied in the direction of manipulators, program-controlled manipulators, manufacturing tools, etc., can solve problems such as re-planning without speed redistribution algorithm, increasing energy consumption, kinematics and dynamics separation, etc.
- Summary
- Abstract
- Description
- Claims
- Application Information
AI Technical Summary
Problems solved by technology
Method used
Image
Examples
Embodiment Construction
[0031] The present invention will be specifically introduced below in conjunction with the accompanying drawings and specific embodiments.
[0032] A multi-constraint machining optimization method for coordinated manipulators based on speed reconfiguration, comprising the following steps:
[0033] Step 1: Construct the dynamics model of the coordinated gripping of the manipulator, simplify the physical model of the workpiece gripped by multiple manipulators, and determine the inertia term, Coriolis force term, and centrifugal force in the manipulator dynamics model through the Lagrangian dynamics method Term and gravitational term, the internal force term of workpiece 4 and calculation method thereof are introduced into dynamic equation to form an equation;
[0034] represents the coupled dynamics model of the processing manipulator 1, the is the generalized inertia term of the processing manipulator system, is the Gothic force term of the processing manipulator system, ...
PUM
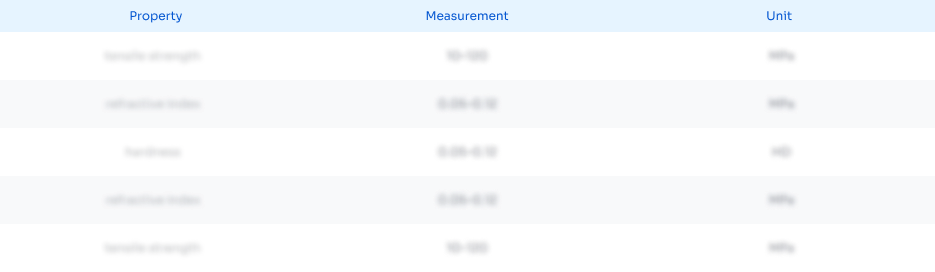
Abstract
Description
Claims
Application Information

- Generate Ideas
- Intellectual Property
- Life Sciences
- Materials
- Tech Scout
- Unparalleled Data Quality
- Higher Quality Content
- 60% Fewer Hallucinations
Browse by: Latest US Patents, China's latest patents, Technical Efficacy Thesaurus, Application Domain, Technology Topic, Popular Technical Reports.
© 2025 PatSnap. All rights reserved.Legal|Privacy policy|Modern Slavery Act Transparency Statement|Sitemap|About US| Contact US: help@patsnap.com