Fatigue life prediction method for geometric discontinuous structure
A fatigue life prediction and geometry technology, applied in sustainable transportation, instrumentation, design optimization/simulation, etc., can solve the problems of lack of universality, complex programming and high computational cost
- Summary
- Abstract
- Description
- Claims
- Application Information
AI Technical Summary
Problems solved by technology
Method used
Image
Examples
Embodiment Construction
[0052] According to the attached Figure 1-9 , give a preferred embodiment of the present invention, and give a detailed description, so that the functions and characteristics of the present invention can be better understood.
[0053] see figure 1 A method for predicting the fatigue life of a geometrically discontinuous structure disclosed in the present invention comprises the following steps:
[0054] S1: Establish a first ABAQUS finite element model of a certain number of grains of a material that is geometrically continuous (that is, without gaps) and that includes the geometrically discontinuous structure, wherein the number of grains is usually multiple, and Define the crystal plastic constitutive equation of the material during the uniaxial fatigue test of the cyclic load through the user subroutine UMAT, so as to obtain the stress-strain relationship of the material under the given cyclic load condition;
[0055] The first ABAQUS finite element model refers to the m...
PUM
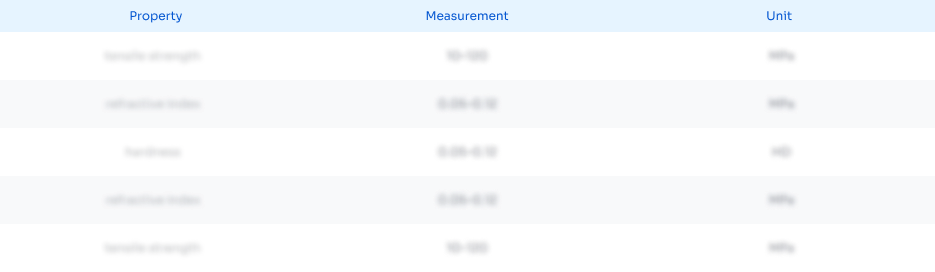
Abstract
Description
Claims
Application Information

- R&D
- Intellectual Property
- Life Sciences
- Materials
- Tech Scout
- Unparalleled Data Quality
- Higher Quality Content
- 60% Fewer Hallucinations
Browse by: Latest US Patents, China's latest patents, Technical Efficacy Thesaurus, Application Domain, Technology Topic, Popular Technical Reports.
© 2025 PatSnap. All rights reserved.Legal|Privacy policy|Modern Slavery Act Transparency Statement|Sitemap|About US| Contact US: help@patsnap.com